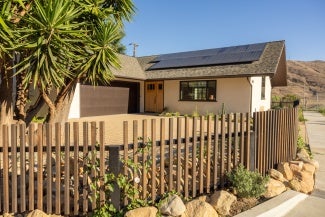
Turning straw into gold: How to cut carbon in residential architecture
As architects and developers get serious about cutting carbon, single-family home construction offers untapped potential.
It sounds like a project out of a fairy tale: a rural home made of straw bale built to withstand harsh Central Washington state winters. But for architect Dylan Johnson, who helped build this structure for his uncle out of straw from a neighbor’s farm, it was a formative experience and introduction to low-carbon construction.
Long aware of the threat of climate change, Johnson found that as better design, materials choices, and renewable energy have made buildings operate more efficiently, the “low-hanging fruit” for cutting carbon emission lay in embodied carbon, or the emission cost of materials and construction. Using straw enabled incredible efficiency and sustainability, with locally sourced material that was actually a carbon sink. In 2021, Johnson even designed a home utilizing straw bale construction for sustainability guru and Patagonia founder Yvon Chouinard in Ventura County, Calif.
“The goal was to make this home as normal as possible and make it look like it's drywall so it would appeal to anybody, even those without the real organic hippie vibe,” he said. “Yvon said it should look like any boring house in the neighborhood.”
Builders need to build these kinds of "boring" homes if the architecture and development worlds want to get serious about cutting their carbon impact. Embodied carbon in the built environment accounts for 11% of global emissions. And while single family homes seem small compared to offices or warehouses, their impact is massive; over half the square footage that gets built in the U.S. every year are small homes, which represent more than half the total emissions, or the same annually as the country of Sweden. And just a handful of regulations and incentives in the United States seek to make drastic cuts to a building’s embodied carbon, most of which are focused on larger buildings and buying cleaner materials.
“You have one chance to reduce embodied carbon when you're building the building,” said Kara Kokernak, senior director of the Urban Land Institute’s decarbonization team. “And depending on what those numbers are, it can overshadow operational carbon.”
But amid these challenges, some see great opportunities for change. The factors that make the industry seem stubborn and stuck in its ways–a market dominated by larger production builders–can be utilized for good, since small changes in methods and materials get adopted and copied, said Chris Magwood, manager of carbon-free buildings at the Rocky Mountain Institute (RMI).
“I see that the opportunity in the homebuilding sector is actually massive compared to the commercial sector,” he said. “Here's a chance in the homebuilding world to intervene in a way where not a very large number of players have an outsized role in making these choices. And once they make them, they keep them.”

Embodied carbon, an increasingly important focal point for commercial design and construction, hasn’t become as much of a rallying cry for residential building. Commercial developers and designers have the benefits of large clients and design firms with resources, the ability to do environmental reports for products and materials, larger pushes for lower carbon cement and green steel, and a track record of success. “The industry is ready,” said Kokernak. Embodied carbon requirements are starting to pop up, including California’s statewide limit for large commercial and school buildings going into effect this July and Marin County, Calif.'s requirement for low-carbon concrete. Groups like the Carbon Leadership Forum and its EC3 tool to measure embodied carbon have started to catalyze change.
Residential architecture and development lacks the same market uptake and procurement power. Even as the COVID pandemic and increased climate disasters have spurred a turn towards more healthy and sustainable living, the shift has been slower for smaller projects. And making all this change at scale in a way that systematically alters how American homebuilding works remains daunting. Customization and experimentation takes additional time and effort, hard sells especially during a time of rising mortgage burdens, higher material and labor costs, and increased price sensitivity during an affordable housing crisis.
"Efficiency, embodied carbon, renewable energy, healthy materials—whatever those very large national or international trends are—take longer to really implement and reinforce on the residential side,” said Jenna Cramer, Green Building Alliance president & CEO.
Luckily, American single-family homes tend to use less glass, steel, and concrete than commercial projects, all emissions-heavy materials. Truly cutting carbon out of these typically wood-framed residential buildings requires swapping out three main internal components, said Nora Wang Esram, senior director for research for the American Council for an Energy-Efficient Economy (ACEEE). Traditional insulation needs to be replaced, and all the plastic that’s often central to low-cost home construction–window frames, furnishings, flooring, PVC piping–has a sizable carbon footprint. Finally, refrigerants can also leak.
One-off solutions can showcase material ingenuity—the ZeroHouse, completed in Ontario, Canada, in 2017 by the Endeavour Centre, features straw bale construction, panelization, helical screws as a stand-in for a typical foundation, and upcycled juice boxes. But cutting embodied carbon at scale requires a larger, systematic approach.
Residential projects that have achieved zero carbon lean towards more experimental or expensive designs, but still hold lessons for more traditional builders and designers. In Malibu, the recently completed Marisol Malibu Zero Series homes achieved net zero operational and embodied carbon via use of local, sustainable lumber, low-carbon concrete, and steel made via electric arc furnaces, becoming just one of just four buildings with the International Living Future Institute’s (ILFI) Zero Carbon Certification.
According to Scott Morris, one of the developers, there’s a green premium for the homes due to utilizing more sustainable items–one of these sprawling, $28.5 million ultra-luxe homes consist of a series of glass-framed ocean view rooms draped in sustainable wood–but the real challenge was getting contractors on board with new methods and materials.
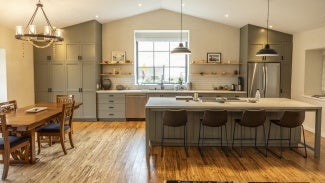
“I’m focused on contractor decarbonization,” said Morris, who’s looking to launch Fortify Fleet, a platform to encourage the industry to adopt more sustainable and even second-hand products when building. “We need to get this to scale. [Contractors] think doing it the way grandpa did it is the right way to go. I actually think the best thing that they can do is to educate themselves and learn and transition their supply chain now, so they can win the jobs of the future.”
The Green Building Alliance wants to help on a more holistic scale with an emerging program called the Appalachian Sustainable Products Network, an effort to encourage a region known for manufacturing homebuilding products to start transitioning to lower carbon options, including more local wood and even hemp. After establishing a network and analyzing the market, the GBA is seeking to sign on owners, developers, and architects, as well as manufacturers, to demonstrate the demand for lower carbon products. Cramer said the aim is to help the region seize a chunk of the estimated $83 billion sustainable building industry.
In addition to material issues, RMI’s Magwood has found that larger builders can go through stages of evaluation of the process–do they need to build new, as opposed to adaptive reuse, can they go smaller, or build denser with row houses, or cut out some materials costs–and slowly shave away embodied emissions. RMI research found swapping out traditional materials with commercially available, affordable, and code-compliant replacements can cut overall carbon footprints, including embodied carbon, by 30% to 50% alone.
The nonprofit launched HomebuildersCAN, a campaign and resource for cutting carbon in homebuilding. RMI worked with Mattamy, a large builder operating in the U.S. and Canada, and helped them simplify a standard home foundation design, cutting it from a dozen corners to eight. The move cut total concrete usage by 20%, increased energy efficiency, and just required one small design change. Another large builder, KB Homes, recently started doing carbon audits and testing new concrete alternatives that could significantly cut down on emissions if a pilot test gets adopted more widely throughout the firm’s operations.
“The exciting thing about the residential space is we see lots of residential buildings that can cut 50% or 60% of embodied carbon versus typical buildings, and they’re doing it today,” Magwood said. This fall, RMI will co-host the first embodied carbon summit for homebuilders. Ideally, the industry begins widespread adoption of such tactics in time to meet drastic needs to draw down emissions in the next decade and beyond.
There are existing models for government funding or interventions that could change the market. Esram points to the General Services Administration, or GSA, which runs the federal government’s real estate portfolio, and often tests new building methods and mandates strict building methods to help spread more sustainable building practices. The GSA has recently focused more on low embodied carbon materials and introduced a roadmap for utilizing them in their own portfolio. A comparable program serving as a test bed for residential homes doesn’t exist yet.
An entire ecosystem for residential construction also needs support, which requires material supply chains along with investments in training. Suppliers need to see value in taking a low-carbon route, architects and practitioners need to be retrained to focus on cutting out embodied carbon, and builders need to see market signals that this is the right building solution to pursue. Adopting more strict building codes could help. But such a change also raises the challenge of equity, and making sure new requirements don’t further impact affordability for a wide swath of homeowners.
“Builders are not being rewarded,” says Esram. “The first movers are early adopters and not being rewarded. They’re doing it for goodwill, and paying more to save the planet, but not everybody has the luxury or the disposable cash to do it.”
To read more about sustainable materials in residential design, click HERE.