MASS MoCA Building 6
The award-winning design for MASS MoCa Building 6 in North Adams, Mass. repairs prior environmental missteps while enhancing its cultural contribution to the community.

- Architectural Credits: Bruner/Cott Architects
- Owner: MASS MoCA
- Location: North Adams, Massachusetts
Project Overview
This project, the third phase of the architect’s work at the Massachusetts Museum of Contemporary Art, bolsters the museum’s world-class reputation while also revitalizing a small New England mill town. The adaptive reuse of Building 6 and a smaller adjacent building has added more than 130,000 square feet of previously undeveloped space to the museum’s sprawling campus for contemporary art, multimedia exhibitions and accompanying events, workshops, and storage.
The project team remediated major contaminants on the site, once a brownfield, promoting the continued healing of the surrounding landscape and adjacent Hoosic River. The building’s transformation also leverages the museum’s location on a peninsula to offer panoramic views of the river and the Berkshire mountains beyond. At this art museum, connections to the outdoors become an important part of the visitor experience.
Building program type(s): Other
Conditioned floor area: 130,550 sq. ft.
Total annual users: 300,080
Site area: 88,550 sq. ft.
Project site: Historic structure or district
Year of substantial completion: 2017
Cost of construction, excluding furnishing: $26,500,000
Framework for Design Excellence
The AIA Framework for Design Excellence represents the defining principles of design excellence in the 21st century. Comprised of 10 principles and accompanied by searching questions, the framework informs progress toward a zero-carbon, healthy, just, resilient, and equitable built environment.
- Equitable Communities
$4.82, 10-year Social Cost of Carbon Intensity ($/gsf)
- Ecosystems
16.9% of the site area was vegetated (landscape or green roof) pre-development
19.1% of the site area is vegetated (landscape or green roof) post-development
2.2% increase in the percent of vegetated area, post-development
0% of vegetated areas are planted with medium to high-quality vegetation
Was the carbon balance of the landscape modeled? No
The site's 10-year landscaping carbon intensity (kg CO2e/sf): N/A
- Water
Stormwater managed on-site: 0%
Water use intensity (gal/sf/year): Benchmark, 26.2; Predicted, 1.9; Measured, [not provided]
Reduction in potable water use from Benchmark: Predicted, 35%; Measured, [not provided]
Total annual water demand met using potable sources: Predicted, 100%; Measured, [not provided]
- Economy
Construction cost per square foot: $200
- Energy
Is the building all-electric? No
Did the project achieve its 2030 Commitment reduction target (80% reduction by 2020)? Yes
Energy Use Intensity, EUI, (kBtu/sf/yr): Benchmark, 95; Predicted, 10.5; Measured, 19.2
Energy Reduction, Exclusive of renewables: Predicted, 79.5%; Measured, 80%
Energy Reduction, Inclusive of renewables: Predicted, 79.5%; Measured, 80%
Type of renewables: None
Carbon Intensity, Operational (kg-CO2e/sf/yr): Predicted, 2.1; Measured, 2.1
Carbon Intensity, Embodied (kg-CO2e/sf/yr): Predicted, 4.6
Total carbon (operational + embodied) over 10 years (kg-CO2e): 3,352,919
- Well-being
30% of the regularly occupied area is daylit (sDA 300/50%)
0% of the regularly occupied area is compliant with glare criteria (ASE 1000, 250)
45% of the regularly occupied area has quality views
Is there occupant control? Yes, in 5 out of 6 categories
Is CO2 measured? No
- Resources
100% of floor area was reused or adapted from existing buildings
Was embodied carbon modeled? Yes
4.6 Predicted embodied carbon intensity (kgCO2e/sf)
0% of the installed wood is FSC certified
- Change:
Was research conducted on likely hazards? Yes, on 3 out of 10 categories
Can the building be used as a safe harbor to support a community during a crisis? [not provided]
Passive Functionality: Partial backup power
How many hours can the building function through passive survivability? [not provided]
Building design lifespan: 1,000 years
Was the building designed for disassembly? Partially
- Discovery:
Commissioning: Yes, Basic only
Post Occupancy Engagement: Yes, in 3 out of 7 strategies
Transparency: Did the team share lessons of the project: Yes, in 6 out of 10 strategies
Who has access to performance feedback: Building operator
MASS MoCA is a world-class museum that is grounded in its place, maximizing the quality of the building and visitor experience. The project revitalizes a small post-industrial New England town and showcases historic mill architecture. Building 6, the third phase of the architect’s work at the museum, expands MASS MoCA, adding 132,000 square feet of gallery and support space. The project also included the renovation of Building 8, a small connected building.
An experienced and integrated team created the design using an iterative design and preconstruction discovery process. For Building 6, the architect approached all aspects of the building design through three actions—editing, weaving, and inserting. These design maneuvers anchor an integrated approach to design that emphasizes intentional transformation in a low-carbon building.
Editing engages the existing building, sculpting and excavating the existing fabric and creating space through removal and reuse. The removal of floors and walls is approached as an operation of architectural cut-and-fill. As material was removed through these sculptural edits, a careful site salvage program was used to stockpile and reuse brick, stone, finish wood, and structural elements to transform the building.
Weaving connects what was and what is to be. Design interventions weave in and out of over 1,000 columns, hundreds of windows, and acres of maple factory floor. Steel stairs cling to walls, bridges span new spaces, and rails mark monumental openings. These weavings do not seek to match the original architecture’s aesthetic, but they match a sense of brawn and open-ended design inspired by the many prior building transformations.
Insertions directly support the art and are tailored for artists and exhibits. These insertions hide building systems, allowing existing fabric to flow through in some moments, and create bespoke inwardly focused environments in others. The galleries are designed as a series of “museums within the museum” for individual artists in an industrial landscape of one-acre floorplates.
Building 6 is part of the overall MASS MoCA campus and serves both global and local communities.
The original Arnold Print Works campus, which finished and dyed textiles, was built between 1860 and 1900. In 1942 the site was sold to the Sprague Electric Company and used for the manufacture of electrical components. Each company was the focal point of the community, and community members of each generation had and have a strong connection to the site and the jobs it provided. When Sprague Electric closed in 1986, it occupied over half the downtown real estate and laid off over 5,000 employees in a city of 20,000. Unemployment skyrocketed and the local economy declined sharply. The buildings and town began to fall apart.
The design of Building 6 extends the reinvention of the historic factory campus as an arts and culture destination. The museum now employs 500 and draws 300,000 visitors each year. It has spurred the development of restaurants, shops, and hotels and has become a center of the community and creative economy. Each year a Community Day offers free admission and community-based events.
Describe the project's approach toward creating an environment that is accessible and welcoming to all and allows everyone to thrive.
While the project attracts visitors from the major metropolitan areas of Boston and New York, and across the globe, it is also deeply connected to its local community. For example, Building 6 sits at the confluence of two branches of the Hoosic River, a feature important to the community. The design includes a monumental unprogrammed space as a place of respite that is capped by a large factory window that frames the moment of confluence. Community members have been vocal in their appreciation of that moment.
Were stakeholders engaged through workshops, meetings, surveys, or other means? If so, what was learned and how does it show up in the design?
Building 6 completes a circulation loop contemplated by the original framework plan. The cultural heritage is on display: Mill and factory features were often untouched and even framed in the design. The wood windows were restored using local labor in an on-site window workshop the museum organized. Similar approaches were used for repairing masonry.
All of the bathroom facilities are all-gender to create a welcoming environment for everyone. This is accomplished with a mix of single-occupant bathrooms and a larger all-gender room with individual stalls and a common hand-washing area.
Was a social site analysis conducted? If so, what was learned and how does it show up in the design?
[NOT PROVIDED]
What does the project do to avoid using materials/manufacturers that perpetuate exploitative labor practices like child and forced labor?
The project was intentional about selecting materials from the region and relies heavily on reused materials from the site.
What did the project do to avoid products that are harmful to the community where they were extracted or manufactured (such as vinyl, tropical hardwood, or natural gas)?
The team avoided Red List materials and materials with harmful chemical compounds on the project.
The social cost of carbon is the burden to humanity that results from carbon emissions. The EPA assumes a value of $190/ton CO2 eq. What is the 10-year Social Cost of Carbon Intensity ($/gsf)?
$4.82, 10-year Social Cost of Carbon Intensity ($/gsf)
Located in the Northern Forest Ecological region, North Adams was settled for its proximity to timber and the Hoosic River, which supported logging and manufacturing operations. Arnold Print Works, the owner of the site at the turn of the 20th century, leveraged its location on a peninsula at the confluence of the Hoosic River. Building 6 was a brownfield site, and through this project major contaminants were remediated, continuing the healing of the natural environment adjacent to a water source. A crawlspace sluiceway, once used to divert dying operations into the river, was remediated and removed.
The transformation features dual panoramic views to the rivers and tree-filled Berkshire mountain range beyond. Unlike at most art museums, the outdoor world is visible and part of the museum experience.
How does the design minimize negative impacts on animals?
Building 6 was primarily an interior architecture project created within the footprint of existing buildings. New exterior lighting was kept to a minimum, and the project is dark sky compliant.
How does the project support biodiversity and improve ecosystem services?
Extensive resources were used to remediate and heal the site, once a brownfield manufacturing site.
How does the project increase carbon sequestration through the landscape?
[NOT PROVIDED]
Metrics
16.9% of the site area was vegetated (landscape or green roof) pre-development
19.1% of the site area is vegetated (landscape or green roof) post-development
2.2% increase in the percent of vegetated area, post-development
0% of vegetated areas are planted with medium to high-quality vegetation
Was the carbon balance of the landscape modeled? No
The site's 10-year landscaping carbon intensity (kg CO2e/sf): N/A
Potable water needs for Building 6 are very low. Since there are already other bathrooms in the museum, only 18 bathrooms were needed in Building 6, all of which use low-flow toilets and lavatories. Shower facilities are provided for employees to support commuting by foot or bicycle.
Building 6’s all-gender facilities were designed to be accessed from the field and the courtyard to accommodate outdoor performances. This reduces the need for portable toilets (that require chemicals and transport) and creates a more dignified experience in a generous light-filled space.
In the courtyard, bottle fill stations are provided for festival use and will support the planned bike path that passes through the building and courtyard.
Describe how the project's stormwater and potable water strategies contribute to site and community resilience.
The project reduces the amount of impermeable area by introducing new vegetated space to a previously 100% impermeable courtyard. Stormwater is collected in the courtyard through catch basins and managed in the existing campuswide stormwater system that is connected to the river and managed by the Army Corp of Engineers. Around the perimeter, the building roof drains directly to pervious areas on the site.
Describe the quality of the water that runs off the site. [NOT PROVIDED]
Describe how and where the project's black water is treated. [NOT PROVIDED]
Metrics
Stormwater managed on-site: 0%
Water use intensity (gal/sf/year): Benchmark, 26.2; Predicted, 1.9; Measured, [not provided]
Reduction in potable water use from Benchmark: Predicted, 35%; Measured, [not provided]
Total annual water demand met using potable sources: Predicted, 100%; Measured, [not provided]
Please explain if a metric requires additional interpretive information.
Building 6 is part of a larger campus served by a large main, so water is not metered separately. The measured water data above is for the main water service and includes not only Building 6 but several other buildings. Even with other connected buildings, water usage is significantly lower than the baseline since museum visitors use shared bathroom facilities distributed throughout the museum and visit Building 6 as a part of their overall visit. In addition, as primarily an interior architecture project, the existing stormwater management systems were not impacted. Therefore, calculations were neither required nor performed.
MASS MoCA’s Building 6 was constructed for $200 per square foot (in 2015 dollars), evidence that the project was designed with economy in mind. This is an order of magnitude lower than most contemporary art museum budgets. The primary strategies in meeting that target included building reuse, treating the large floorplates as landscapes with targeted interventions, and removing damaged elements rather than repairing them. New materials were limited to new interventions and enclosures, and 100,000 kg of material was salvaged and incorporated into the design. Superfluous new materials were avoided.
The design process included integrated cost estimating by two parties to stay on target. The project leveraged state funding for both economic development and culture along with philanthropic gifts.
In thinking about the future, durable low-maintenance materials were used throughout, and the building was designed to continue its evolution with changing, site-specific installations. A low EUI, efficient mechanical system, and LED lighting keep operational costs low.
How does this project contribute to local and/or disadvantaged economies?
MASS MoCA is a museum for everyone. The familiar buildings and sense of discovery present world-class art without exclusivity or pretense. There is active community participation in a city where the poverty rate is 40% greater than the state average. MASS MoCA offers free days programmed with inviting events for the local and broader community. Partnerships with local schools were forged early and continue to evolve and grow. Fully subsidized programs serve several area school districts and multiple age groups, and offer support for educators.
How did design choices reduce system sizes and minimize materials usage, allowing for lower cost and more efficiently designed systems/structure?
Reuse is this project’s cornerstone. Only a fraction of the materials used for Building 6 are new, with the vast majority preserved in place or salvaged on-site, repaired and reconfigured over time. Galleries—or museums within the museum—are tailored to the art they hold, allowing smaller systems throughout by containing and reducing those spaces that require tighter set points. The rest accept expanded comfort ranges.
How did life cycle cost analysis influence the project's design?
Durability and changeability were assessed in each design element depending on its relative permanence in a museum built for change.
Cost
Construction cost per square foot: $200
Museums typically use a lot of energy in their operations, but Building 6 has a measured EUI of 19.2, 80% less than the benchmark.
Electric sources provide 88% of operating energy. The primary heating and cooling are achieved with all-electric VRF systems distributed throughout. Dedicated outdoor air systems utilize hot water from the museum’s central boiler plant.
Humidity control is limited to one gallery, a “box within a box.” While the exterior walls were not insulated, thermal upgrades were prioritized at the roof and interior storm windows. Thermal mass, LED lighting, and daylighting contribute to the low EUI. Energy modeling was conducted in the design process, and the building was fully commissioned.
The building has a 200 kw solar array on its roof, part of a larger solar array covering other campus roofs. Data specific to the Building 6 array cannot be extracted and has not been included in the measured EUI calculation. PV watts software predicts that the array would produce 203,000 kwh of renewable energy annually in this climate. Approximately 25% of the campus’s energy, including for Building 6, comes from on-site solar arrays throughout the campus.
Describe any energy challenges associated with the building type, intensity of use, or hours of operation, and how the design responds to these challenges.
Museums routinely use outsized amounts of energy to achieve design standards based on tight temperature, humidity, and light control. In a turn-of-the-century mill building, such an approach is untenable. The team worked with the client to understand the actual requirements of the art to be shown, concluding that most of the art could be displayed in natural light and a wider range of conditions.
Metrics
Is the building all-electric? No
Did the project achieve its 2030 Commitment reduction target (80% reduction by 2020)? Yes
Energy Use Intensity, EUI, (kBtu/sf/yr): Benchmark, 95; Predicted, 10.5; Measured, 19.2
Energy Reduction, Exclusive of renewables: Predicted, 79.5%; Measured, 80%
Energy Reduction, Inclusive of renewables: Predicted, 79.5%; Measured, 80%
Type of renewables: None
Carbon Intensity, Operational (kg-CO2e/sf/yr): Predicted, 2.1; Measured, 2.1
Carbon Intensity, Embodied (kg-CO2e/sf/yr): Predicted, 4.6
Total carbon (operational + embodied) over 10 years (kg-CO2e): 3,352,919
Please explain if a metric requires additional interpretive information.
Electricity and natural gas use are metered and data is collected from 2021 utility bills. The design relies on a small amount of hot water from the central boiler plant, which is not metered. The team included the modeled amounts for hot water in the measured table in order not to skew the comparative results. The solar production is also tied to a larger system from which the team was unable to parse separate production data. The team chose not to include solar production in the measured data but estimate that the portion of the campuswide system on the Building 6 roof produces 203,000 kwh annually (or 3.4 kbtu/sf/year) based on modeled results.
MASS MoCA transformed a vast site of deteriorated historic structures used for manufacturing into a clean, safe, and pleasurable destination. The design is welcoming and filled with perimeter and overhead daylight. Views to nature are abundant in the art-filled and generous circulation spaces and in some enclosed gallery spaces. The building design encourages movement and activity in an organic flow, with one-acre floorplates and a series of enticing stairs for vertical circulation.
Natural materials are featured throughout, including the reused timber structure, reused maple flooring, reused limestone, and reused brick, which are all well-worn and beautifully patinated. Two key moments in the design call on biophilic principles. First, the “prow” calls on prospect and refuge, creating a special moment to pause and observe the river branch’s confluence. The overall plan organization relies on the integration of parts to the whole (museums within the museum), with the center lightwell serving as a central focal point and reorientation device.
The HVAC system includes a dedicated outdoor air system with heat recovery and MERV 13 filtration.
The design team drew on its experience with a concurrent Living Building project to specify healthier building materials where new materials were required.
Was a chemicals of concern list or other third-party framework used to inform material selection? If so, how?
Building 6 prioritizes specification of materials that are simple and elemental. Composite materials containing chemical compounds were avoided. Coatings were selected to reduce the introduction of VOCs and other chemicals.
How did the project advocate for greater transparency in building material supply chains?
Many of the materials used at MASS MoCA come from MASS MoCA. Highlighting salvaged materials and the work of staff and local tradespeople builds on a local and on-site history of intervention in the buildings that the architect hopes will stretch far into the future.
Metrics
30% of the regularly occupied area is daylit (sDA 300/50%)
0% of the regularly occupied area is compliant with glare criteria (ASE 1000, 250)
45% of the regularly occupied area has quality views
Is there occupant control? Yes, in 5 out of 6 categories
Is CO2 measured? No
The design for MASS MoCA Building 6 deeply considers embodied carbon. It maximizes the conservation of materials in place, utilizes site-salvaged materials, and uses a limited palette of new materials. Key spaces in the museum are created by sculpting space out of the building. Materials removed in this process were carefully stockpiled and reused—an architectural cut-and-fill operation that reduced waste and avoided the need for any virgin brick, stone, structural wood, or finish wood.
Working with found material kept the project within regional material economies that have existed since the original construction and in alignment with the museum’s mission as a regional job creator that celebrates local craft. For example, the team worked carefully with masons to modify openings in the load-bearing masonry walls. Repaired and replaced factory windows were fabricated on-site in the museum’s window shop, which has been in operation since 1999.
Did embodied carbon considerations inform the design? How?
The result is a museum constructed using 4.6 kgCO2eq/sf, a remarkably low carbon expenditure compared to the deQO Database Average of 38.8kgCO2eq/sf.
Embodied and total carbon were key considerations in the design of Building 6. The design works with the existing building, transforming it at strategic points with outsize impact. New material is added only where existing material cannot be transformed to suit the new function. Over 12,000,000 kg of materials were left in place, and another 100,000 kg of materials were salvaged and reused on-site.
Did the idea of circularity/circular economy inform the design? How?
MASS MoCA embodies the idea of a circular economy. As a factory, first of textiles and later electronics, the building has been used, modified, and reused countless times. Its transformation into a museum continues this legacy of building and material reuse, which extends to new material selections.
Describe any special steps taken during design/construction to make disassembly, deconstruction, or reuse easier at the building's end of life.
The architect, design team, and client carefully considered future reuse on several time scales. As a non-collecting museum and art fabricator, making and remaking is part of MASS MoCA’s ethos. Its exhibits, whether they are installed for six months or 20 years, are rotating, varied, and highly specific. They are often designed and built to suit the space but just as often require change to the architecture itself. The design maintains and advances low-tech, elemental solutions—bricks, wood beams, wood decking, solid wood floors, and simple partitions—that can be disassembled, modified, and reassembled by local tradespeople and, often, museum staff. Long life and change reinforce each other.
Metrics
100% of floor area was reused or adapted from existing buildings
Was embodied carbon modeled? Yes
4.6 Predicted embodied carbon intensity (kgCO2e/sf)
0% of the installed wood is FSC certified
Please explain if a metric requires additional interpretive information.
MASS MoCA Building 6 relies heavily on materials salvaged and reused on-site (>100,000 kg) and materials left in place (>12,000,000 kg). These materials are in effect zero cost (excluding labor) but comprise the vast majority of materials utilized. All of the finish wood, structural wood, brick, and stone are salvaged.
Change is part of MASS MoCA’s story. The site reflects four eras of significant social and economic change. At different times, it has been a regional anchor for logging, textiles, and electronics production, and it now anchors the cultural economy. Building 6 itself was changed incrementally over time, and the design works to frame many of those moments. For example, with the onset of electric lighting, the center lightwell was closed in. This renovation reopened the lightwell but left the paint patterns on the brick that highlight the infilled rooms.
The inherited mill structure is inherently flexible, and the design for Building 6 anticipates further change, reflecting the loose fit, long life principle. All of the gallery walls are nonbearing and could be reconfigured in the future.
In what ways does the design anticipate climate change over the life of the building?
In anticipation of a decarbonized grid, the project was designed so that 88% of its energy comes from electric sources. Fossil fuels are used only for domestic hot water and hot water coils in the ventilation units. These could be replaced by electric versions in the future. In addition, the design focused on the total carbon picture, reflecting the urgency of carbon reduction in the short term.
How does the design anticipate restoring or adapting function in the face of stress or shock, such as natural disasters, blackouts, etc.?
A 150 kw standby generator is part of the design, allowing lighting and some HVAC to function during a power outage. Building 6 was upgraded to meet seismic codes through the introduction of a series of seismic braces.
Metrics
Was research conducted on likely hazards? Yes, on 3 out of 10 categories
Can the building be used as a safe harbor to support a community during a crisis? [not provided]
Passive Functionality: Partial backup power
How many hours can the building function through passive survivability? [not provided]
Building design lifespan: 1,000 years
Was the building designed for disassembly? Partially
Building 6 has a strong sense of discovery and delight. Visitors smile as they amble along the circulation paths, carefully designed staircases and bridges, and linked spaces. The scale of a human being compared to this edited factory architecture is unusual. Figure eights and loops create unique experiences and volumetric changes that cause one to see the building in different ways. At the same time, visitors are encountering site-specific art that presents its own delight and discovery.
As the third phase of MASS MoCA, Building 6 is both an evolution of ideas refined by the museum and architect over several decades and a fertile testing ground for new ideas. Much of the industrial-inspired detailing builds on a legacy of transformation, but Building 6’s vast, intact floorplates inspired new thinking and offered new opportunities for creative horizontal sculpting.
The project’s stories and lessons have been shared broadly. The entire architecture firm visited the site upon completion, and approaches from this project inform the firm’s subsequent work. Stories have been shared in dozens of local, regional, and national articles and in a series of building tours for architects, preservationist groups, the local community, and architecture students.
What lessons learned through this project have been used to improve subsequent projects?
Approaches to quantifiable life cycle assessment, especially of embodied and total carbon, have allowed the team to focus on transformative reuse and high-performance building design. After the groundbreaking work on Building 6, the team now routinely uses life cycle assessment as part of the design and analysis of their projects. Rich discussions on combinations of new and old have informed design approaches on other transformation projects.
If a post-occupancy evaluation was conducted, describe the process and outcomes.
While we are able to collect basic utility data for electric and natural gas consumption, collecting water and solar data proved difficult since those systems have been designed as larger, campus-scale systems. The team continues to work with the museum facilities team to find ways to measure and improve performance.
If a post-occupancy performance testing was conducted, describe the process and outcomes.
[NOT PROVIDED]
If energy and/or water modeling was performed, describe any differences between predicted and measured use.
[NOT PROVIDED]
Metrics
Commissioning: Yes, Basic only
Post Occupancy Engagement: Yes, in 3 out of 7 strategies
Transparency: Did the team share lessons of the project: Yes, in 6 out of 10 strategies
Who has access to performance feedback: Building operator
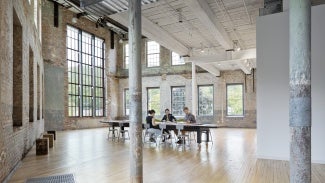
Explore additional images, detailed drawings, and diagrams for a visual narrative of architectural innovation integrating exemplary performance with a compelling design.
Project team & jury
Architect: Bruner/Cott Architects
Construction Manager: Gilbane Building Company
Engineer - Structural: Arup
Engineer - Mechanical, Plumbing, Fire Protection: Petersen Engineering
Engineer - Electrical, Fire Access: R.W. Sullivan Engineering
Engineer - Civil: Hill Engineers, Architects, Planners, Inc.
Consultant - Code: Cosentini Associates
Consultant - Specifications: Kalin Associates
Consultant - Environmental: GZA GeoEnvironmental
Consultant - Acoustic: Acentech
Consultant - Lighting: Lumen Studio
Consultant - Lighting Design: Collaborative Lighting
Consultant - Cost Estimating: Daedalus
Engineer - Fire Protection: Fire Protection Services
Consultant - Food Service: Colburn Guyette
Consultant - Hardware: ASSA ABLOY
Consultant - Structural Wood Testing: Wood Advisory Services, Inc.
Consultant - Existing Conditions Scanning: Existing Conditions Surveys, Inc.
Consultant - Environmental Graphics: Over,Under
Nadine Saint-Louis, AIA, Chair, McHarry Associates, Miami
Yu-Ngok Lo, FAIA, YNL Architects, Culver City, Calif.
Jack Rusk, Assoc. AIA, EHDD, San Francisco
Eddy Santosa, AIA, Mott MacDonald, Los Angeles
The COTE® Top Ten Award is the industry’s best-known award program for sustainable design excellence.
Explore projects setting the standard in design and sustainability, presented by the Committee on the Environment.