PAE Living Building
The award-winning design for PAE Living Building in Portland, Ore. serves as a model for bridging sustainable design and profitability in commercial office space.
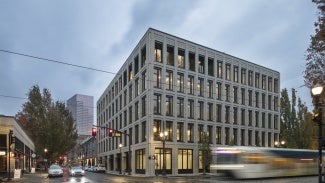
- Architectural Credits: ZGF Architects
- Owner: Edlen & Co
- Location: Portland, Oregon
Project Overview
Located in Portland, Oregon, PAE Living Building is the first developer-driven and largest commercial office Living Building in the world, proving that such projects are not only technically possible on dense urban sites but also financially viable opportunities for investors. The project generates 108% of its energy needs on-site through two systems, a solar array on its own rooftop as well as one gifted to an affordable housing project six miles away. It’s one of the first buildings in the city to install a photovoltaic-powered battery storage system that features a two-way connection to Portland’s grid, allowing the building to give back to the city while bolstering its own resiliency.
Designed to last 500 years, the project and its innovations demonstrate the highest levels of sustainable design and endeavor to inspire change. Since its opening in 2021, it has welcomed thousands of people from around the world, including trade professionals, policymakers, and students eager to learn more about its construction and systems.
Building program type(s): Office – 10,001 to 100,000 sq. ft.
Conditioned floor area: 57,331 sq. ft.
Total annual users: 15,000
Site area: 11,700 sq. ft.
Project site: Previously developed land, Historic structure or district
Year of substantial completion: 2021
Cost of construction, excluding furnishing: $25,200,000
Framework for Design Excellence
The AIA Framework for Design Excellence represents the defining principles of design excellence in the 21st century. Comprised of 10 principles and accompanied by searching questions, the framework informs progress toward a zero-carbon, healthy, just, resilient, and equitable built environment.
- Equitable Communities
$10.48, 10-year Social Cost of Carbon Intensity ($/gsf)
- Ecosystems
[Project is zero lot line]
0% of the site area was vegetated (landscape or green roof) pre-development
1.5% of the site area is vegetated (landscape or green roof) post-development
1.5% increase in the percent of vegetated area, post-development
100% of vegetated areas are planted with medium to high-quality vegetation
Was the carbon balance of the landscape modeled? No
The site's 10-year landscaping carbon intensity (kg CO2e/sf): [N/A]
- Water
Stormwater managed on-site: 100%
Water use intensity (gal/sf/year): Benchmark, 13.6; Predicted, 0; Measured, 0
Reduction in potable water use from Benchmark: Predicted, 100%; Measured, 100%
Total annual water demand met using potable sources: Predicted, 0%; Measured, 0%
- Economy
Construction cost per square foot: $435
- Energy
Is the building all-electric? Yes
Did the project achieve its 2030 Commitment reduction target (80% reduction by 2020)? Yes
Energy Use Intensity, EUI, (kBtu/sf/yr): Benchmark, 86.1; Predicted, 19.7; Measured, 16.8
Energy Reduction, Exclusive of renewables: Predicted, 77%; Measured, 80%
Energy Reduction, Inclusive of renewables: Predicted, 101%; Measured, 99%
Type of renewables: On-Site + Off-Site
Carbon Intensity, Operational (kg-CO2e/sf/yr): Predicted, 2.2; Measured, 1.9
Carbon Intensity, Embodied (kg-CO2e/sf/yr): Predicted, 36.2
Total carbon (operational + embodied) over 10 years (kg-CO2e): 3,162,614
- Well-being
65% of the regularly occupied area is daylit (sDA 300/50%)
0% of the regularly occupied area is compliant with glare criteria (ASE 1000, 250)
100% of the regularly occupied area has quality views
Is there occupant control? Yes, in 5 out of 6 categories
Is CO2 measured? Yes, 900 ppm is the design goal for maximum CO2
- Resources
0% of floor area was reused or adapted from existing buildings
Was embodied carbon modeled? Yes
36.2 Predicted embodied carbon intensity (kgCO2e/sf)
100% of the installed wood is FSC certified
- Change:
Was research conducted on likely hazards? Yes, on 7 out of 10 categories
Can the building be used as a safe harbor to support a community during a crisis? Yes
Passive Functionality: Partial backup power
How many hours can the building function through passive survivability? 2,400
Building design lifespan: 500 years
Was the building designed for disassembly? Partially
- Discovery:
Commissioning: Yes, Basic, Enhanced, On-going
Post Occupancy Engagement: Yes, in 7 out of 7 strategies
Transparency: Did the team share lessons of the project: Yes, in 10 out of 10 strategies
Who has access to performance feedback: All occupants
Designed and engineered to last 500 years, the PAE Living Building is the first developer-driven and largest commercial office Living Building in the world.
The five-story building proves the financial viability of developing mixed-use commercial structures that improve both their urban and ecological context. Its aesthetic appeal and sustainability approach are rooted in simplicity, showcasing how high-performance design can positively impact people and planet.
Built on an existing parking lot in Portland, Oregon’s Old Town Historic District, the project was required to respond to detailed district regulations addressing aesthetics and material selection. With a nod to the style and scale of the surrounding structures, the building’s design utilizes the golden ratio, based on the Fibonacci sequence, as a proportional guide. Found both in nature and classical architecture, the golden ratio proportions create a facade that is aesthetically pleasing, respects the historic district, and is both modern and timeless.
The design seamlessly integrates complex systems to support superior levels of occupant comfort and productivity while using less energy, water, and material than comparable buildings. All the PAE Living Building’s needs are met via on-site water capture and solar arrays that generate 108% of the annual energy necessary to operate the building. One of the first buildings in Portland with a PV-powered battery storage system with a two-way connection to the city grid, the building gives energy back to the city, while the batteries provide resiliency and manage the back-feeding restrictions in the downtown electrical grid.
The entire building’s water needs are met via captured rainwater that is treated on-site. A 71,000-gallon underground cistern is sized for use even in low water years, and water captured on ground-level canopies is channeled into planters along the building edge. The building is disconnected from the city water and sewer system, utilizing a multistory-vacuum-flush toilet system that transforms waste into a nutrient-rich resource.
Occupant comfort and health are prioritized in every system and material. Operable windows allow the interior environment to fully open to the exterior on the east and south façades, drawing in fresh air and light. A “deckony” on the top floor of the building is the social heart of the building, combining the views one would get from a rooftop deck with the protection of a covered balcony. Exposed mass timber beams, which reduce embodied carbon emissions by 40%, provide a sense of warmth while also serving as the structure of the building. Simple and clean concrete topping slabs provide comfortable radiant heating and cooling. Healthy Red List–free material selections, daylighting, biophilic elements, and ventilation strategies all support a productive, healthy workplace.
The PAE Living Building proves that meeting the highest sustainability standards for new buildings is financially viable in a developer-driven model. It shows Portland and the rest of the world what is possible in commercial development.
The PAE Living Building’s urban site proved conducive to a regenerative building that serves its community. The project creates a human-scale environment where one is lacking, restoring a piece of the walkable, transit-oriented neighborhood. Previously a private parking lot, the five-story office building relies on its access to nearby transit and bike paths to eliminate the need for parking. The building boasts 85% occupancy and is comprised of certified B Corp and nonprofit tenants.
In keeping with historic guidelines, rooftop solar panels had to be hidden from view, limiting energy generation on-site. To resolve this challenge and meet solar needs for net zero energy, the project funded an array on the Renaissance Commons affordable housing project six miles to the north. The project donated the panels and electricity and subscribed to 100% renewable electricity through the local utility. This arrangement increased the amount of renewable energy in the region while financially benefitting the affordable housing operator.
To honor the history and people who first lived on the site, the project commissioned artwork from Toma Villa, a Portland-raised member of the Yakama Nation. Villa’s wood carving and inscribed motif of indigenous basketry designs welcome visitors.
Describe the project's approach toward creating an environment that is accessible and welcoming to all and allows everyone to thrive.
The PAE Living Building gives occupants control over thermal comfort, ventilation, daylight, and views. All regularly occupied areas have views to the outside, and occupants are connected to nature at every level of the building, from the ground plane to the top floor, supporting both occupant health and productivity. The team avoided finish materials and plastic laminates that are both harmful in their manufacturing and off-gas and affect indoor air quality upon installation. Air quality was tested pre- and post-occupancy to ensure compliance with Living Building Challenge’s stringent standards.
Were stakeholders engaged through workshops, meetings, surveys, or other means? If so, what was learned and how does it show up in the design?
Externally, the project closely engaged the Old Town Historic Community Association to understand its needs and met frequently with the Historic Commission, which oversees Historic District development. These conversations helped the team understand how the project could support the surrounding people and businesses, including historically underserved communities. PAE continues to volunteer in the community and offers its meeting space free to community members focused on equity and sustainability.
For building occupants, guidance is written into each lease to ensure ongoing occupant behavior supports the building’s operational performance goals, and future tenant improvements strive to meet Living Building Challenge requirements.
Was a social site analysis conducted? If so, what was learned and how does it show up in the design?
A comprehensive site analysis addressed the history and current context of the site to ensure the building honored the historic, indigenous practice of ecological stewardship and the architectural traditions of the historic Old Town neighborhood. The analysis revealed the role native tribes historically played in achieving balance and integration with the natural environment as well as the underlying proportional relationships of the district’s architecture that are rooted in nature and the Fibonacci series. As a result, street and indigenous art were included throughout the design, and neighborhood-inspired facade proportions support effective daylighting and views.
What does the project do to avoid using materials/manufacturers that perpetuate exploitative labor practices like child and forced labor?
The Material Petal is one of the Living Building Challenge’s most challenging aspects. The team prioritized local and regional materials and utilized a rigorous materials vetting framework to ensure Red List–free materials or fully reviewed exceptions were utilized to avoid potential health impacts to all populations affected by the material manufacturing life cycle. Of the 942 products installed, 476 are verified Red List–free and 22 are salvaged and reused materials. Where no Red List–free products could be found, the team challenged 391 manufacturers to consider modifying their product ingredients to expand market availability of healthy materials.
What did the project do to avoid products that are harmful to the community where they were extracted or manufactured (such as vinyl, tropical hardwood, or natural gas)?
The team avoided substances noted on the Living Building Challenge Red List, a collection of chemicals known to cause harm to people and the environment. This meant rigorous screening of all materials, requiring material ingredient transparency documentation (with some necessary exceptions) and narrowing the materials palette and specifying more bio-based products like mass timber for structural elements and wool textiles for the interiors. The fully electric building focused on clean energy sources, converting all human waste to productive use and avoiding finish materials, such as plastic laminates, that are harmful in manufacturing or negatively affect indoor air quality.
The social cost of carbon is the burden to humanity that results from carbon emissions. The EPA assumes a value of $190/ton CO2 eq. What is the 10-year Social Cost of Carbon Intensity ($/gsf)?
$10.48, 10-year Social Cost of Carbon Intensity ($/gsf)
The PAE Living Building is designed as an ecosystem. From capturing rainwater to supply of all water needs to a first-of-its-kind urine-to-fertilizer system, the building’s closed-loop systems ensure resilience while reducing the impact on city and regional systems.
As the building is designed to last 500 years, the project team took great care to determine how the building could support changes in occupant needs over generations and remain resilient in the face of a changing climate.
Energy and water systems mimic natural processes, while the design honors natural systems by considering how air, water, and light move through the structure to nurture both the building and its occupants. Occupants directly interact with these systems. The top-floor “deckony” is made available to the local sustainability and green building community for panels and get-togethers, and tours of the building help enrich the community just as much as the industry visitors, providing ongoing education and awareness for all who pass through.
How does the design minimize negative impacts on animals?
The project meets Portland’s bird-safe requirements, limiting glazing to less than 30% of facades, with punched openings in masonry walls. The team also eliminated exterior up-lighting.
How does the project support biodiversity and improve ecosystem services?
To help ensure biodiversity and preservation beyond the building site, the project team worked with the International Living Future Institute’s (ILFI’s) Habitat Exchange program to purchase an acre of conservation forest land. On-site, the team partnered with Alvéole, urban beekeepers, to care for a honeybee hive on the rooftop. The bees pollinate flowers within the vicinity. Additionally, a first-of-its-kind fertilizer system transforms waste to nutrient sources for plants and is available at local nurseries.
How does the project increase carbon sequestration through the landscape?
As a zero-lot line building, the project has a very limited landscape. In the available space on the two street sides of the building, the team replaced trees that had been removed for construction. The tree removal was done sustainably, with an urban tree salvage company recovering usable wood, sequestering the carbon for the foreseeable future. The wood was turned into a reception desk, cabinet pulls, and end tables for the third-floor lobby. Edible plantings on the fifth floor “deckony” provide seasonal sustenance to occupants, and ground-level planters add to the urban canopy.
Metrics
0% of the site area was vegetated (landscape or green roof) pre-development
1.5% of the site area is vegetated (landscape or green roof) post-development
1.5% increase in the percent of vegetated area, post-development
100% of vegetated areas are planted with medium to high-quality vegetation
Was the carbon balance of the landscape modeled? No
The site's 10-year landscaping carbon intensity (kg CO2e/sf): [N/A]
Please explain if a metric requires additional interpretive information.
The project is a zero lot line building. The vegetated area includes planters on the ground level lobby and retail entry recesses, as well as urban agriculture planters on the 5th floor "deckony" area. Also, trees and tree planters are not included in the above metrics, as these are in city ROW and not within the project's defined site area.
The PAE Living Building is fully disconnected from city water and sewer systems. A 71,000-gallon underground cistern collects rainwater, which is filtered in its own water district, one of two in the city. While Portland’s total annual rainfall is enough to serve the building, minimal rain during the summer months necessitated sufficient storage. When rain falls, including the precipitation that runs off the PV panels, it flows to one of three drains placed on the slightly graded rooftop. It is then channeled through the building core toward the cistern located underneath the ground floor. First-of-their-kind multistory vacuum-flush compostable toilets reduce water use and transform waste into a nutrient-rich fertilizer. The vacuum flush system also allows for more flexibility in the placement of both the restrooms and composters since they no longer need to be in vertical alignment.
Currently, the only option in downtown Portland for excess water is the combined stormwater sewer system. Though the small amount of excess water is highly treated before leaving the site, the building includes both storm and waste pipes leading from the site to accommodate potential future upgrades to city infrastructure.
Describe how the project's stormwater and potable water strategies contribute to site and community resilience.
Scarcity of potable water is an increasing risk, even in regions with a historic abundance of fresh water. The project eliminated reliance on the city water system, capturing all the water it needs on-site. Captured water is treated for potability, with water pumped from the cistern through a treatment system and back to potable and non-potable building systems. After water is treated to potable standards, it flows through hot and cold water pipes leading to sinks and lavatories throughout the building’s five floors and to showers on the ground floor.
Describe the quality of the water that runs off the site.
All discharge is treated to a high level before it leaves the site. When the cistern reaches capacity, excess stormwater is diverted to the municipal sewer since it cannot be infiltrated on-site for several reasons. The site is in a dense historic urban area, blocks from the Willamette River, with seasonally high groundwater and tight soils, eliminating the opportunity for on-site infiltration and groundwater recharge.
Describe how and where the project's black water is treated.
The building’s blackwater is channeled through two separate, dedicated drain lines. Liquid waste from the 14 waterless urinals flows into a 1,000-gallon nutrient recovery tank. Water from toilets carries waste to one of 20 composting bins located on the first floor. Leachate generated from the compost bins is then collected in a 2,000-gallon tank. By producing liquid fertilizer and agriculture-grade compost on-site, the circular system offers another income source for the building owners.
Metrics
Stormwater is managed on-site. 100%
Water use intensity (gal/sf/year): Benchmark, 13.6; Predicted, 0; Measured, 0
Reduction in potable water use from Benchmark: Predicted, 100%; Measured, 100%
Total annual water demand met using potable sources: Predicted, 0%; Measured, 0%
Please explain if a metric requires additional interpretive information.
Reported numbers for actual usage cover September 2022 to August 2023.
The building has composting toilets that use 0.12 gallons of water per flush that then goes to the composters. Additionally, the waterless urinals are part of a nutrient-recovery system in which the urine is collected, batch-processed into fertilizer, and sold at local nurseries.
Captured rainwater is not directly metered. Instead, the 71,000-gallon cistern tank level is monitored, and treated rainwater to the daytanks is metered. Numbers reported are thus treated rainwater to the daytanks. The building operates fully on captured rainwater treated to potable standards for all water uses. The cistern was sized to maintain net zero water operation year-round, even during the dry summer months. In addition, the cistern has the capacity to manage a Portland two-year, 24-hour storm (2.4 inches), holding this volume and slowly releasing it into the public storm sewer after the storm event. Additionally, a greywater system collects water from sinks and showers, treats it, and then distributes it to water closets and to the balcony for garden irrigation. Currently, the greywater system is not fully operational. Over the past year, the building has used collected rainwater for the flush fixtures and irrigation with plans to switch over once the treatment system is fully functional.
The project embodies PAE’s mission to accelerate change through technical excellence and innovation. One of the primary project objectives was to prove the viability of developing commercial mixed-use structures that benefit their ecological and urban environments while delivering financial returns.
The project finances were an important part of getting the development off the ground. Through the effort and investment of the main partners, one of which is the anchor tenant, the financials penciled out. This worked out because the partners offered their fees as equity in the project, and the development location is in one of Portland’s 11 Opportunity Zones. The proforma anticipated a 10% internal rate of return over a 10-year hold and a 10% rent premium. Since the building far exceeds current code minimums and is designed to last 500 years, the 10-year hold requirement was not a barrier for investors. Rent premiums are supported by tenant expectations that the Living Building supports employee retention and recruitment efforts as well as increased productivity.
The PAE Living Building proves that similar projects are not only technically possible on a dense urban site but also financially viable opportunities for private investors.
How does this project contribute to local and/or disadvantaged economies?
The team funded an off-site PV array on the Renaissance Commons affordable housing project just six miles away. The donation translates to approximately $20,000 annual savings in electric costs for Renaissance Commons, which REACH Community Development can now devote to other services. REACH also owns the PV array outright.
How did design choices reduce system sizes and minimize materials usage, allowing for lower cost and more efficiently designed systems/structure?
Among the many benefits of a wood-framed building is the structural system, which is both a durable material and beautiful finish. Wherever possible, the team left structural materials exposed to also serve as the finish material.
How did life cycle cost analysis influence the project's design?
While the project is more expensive than a traditional developer office building, the benefits provided by a Living Building Challenge structure make the full life cycle costs pencil out. This includes energy and water savings, longevity, adaptability, resilience, and an improved occupant experience, all of which translates to higher value for the tenants and developer-owners.
Cost
Construction cost per square foot: $435
The PAE Living Building produces 108% of its energy needs on-site via two systems: an on-site rooftop solar array and an off-site array gifted to an affordable housing project. Designed for an EUI of 19.5, the building can operate completely disconnected from the grid for at least a week and up to 100 days in the summer months.
Solar arrays generate net positive energy, while a connection to the city grid enables the structure to give back. The project is one of the first buildings in Portland to install a PV-powered battery storage system, allowing two-way power connection to the city’s utility network and electrical grid.
Natural ventilation and a tight building envelope mean significantly less energy is used for heating and cooling, translating to a 53% energy savings over code. The team also sought to optimize everything that uses energy in the building. To reduce loads, tenants modified work settings to utilize low-energy monitors and laptops and moved most traditional IT infrastructure to a “green cloud.”
Initial data shows the building is performing as intended. During a 12-month period ending August 2023, the project generated 306,300 kWh and used only 281,600 kWh, creating 8.7% more energy than the building used.
Describe any energy challenges associated with the building type, intensity of use, or hours of operation, and how the design responds to these challenges.
The historic district requirements meant solar could not be visible, reducing available space to support the structure’s energy needs. The team’s solution to these restrictions resulted in scale-jumping, siting an additional off-site solar array on a nearby affordable housing project. This expanded overall renewable energy in the region while donating $20,000 annually in electricity expenses (as well as the physical panels). The building’s resulting reduced rooftop array is configured in alternating waves of east- and west-facing panels to capture sunlight during both morning and afternoon hours and allow for a greater number of panels per unit area.
Metrics
Is the building all-electric? Yes
Did the project achieve its 2030 Commitment reduction target (80% reduction by 2020)? Yes
Energy Use Intensity, EUI, (kBtu/sf/yr): Benchmark, 86.1; Predicted, 19.7; Measured, 16.8
Energy Reduction, Exclusive of renewables: Predicted, 77%; Measured, 80%
Energy Reduction, Inclusive of renewables: Predicted, 101%; Measured, 99%
Type of renewables: On-Site + Off-Site
Carbon Intensity, Operational (kg-CO2e/sf/yr): Predicted, 2.2; Measured, 1.9
Carbon Intensity, Embodied (kg-CO2e/sf/yr): Predicted, 36.2
Total carbon (operational + embodied) over 10 years (kg-CO2e): 3,162,614
Please explain if a metric requires additional interpretive information.
Reported numbers are for September 2022 to August 2023. The utility meter is a net meter. However, additional meters track production and energy usage, and gross numbers are reported here.
This project is operating at verified net zero (positive) energy, per the Living Building Challenge guidelines, with the energy production on-site (limited by available roof area in the project’s historic district, as well as export limitations within the downtown grid) and off-site (located on another Portland building served by the same electrical utility) exceeding annual usage.
The PAE Living Building is designed to take care of its occupants. The building supplies more fresh air than required by code, using DOAS mechanical ventilation with radiant floors to provide primary seasonal heating and cooling. Outside air flows through occupied spaces via manually operable and automatic windows, giving occupants control over both the ventilation and daylight. An inviting mass timber staircase features tunable lighting and windows, and an on-site gym and bike storage are accessible to all occupants. The neighborhood’s walkability and considerable public transit access enables easy commutes.
The fifth-floor “deckony” is the building’s social heart, combining the view one would get from a rooftop deck with the added protection of a balcony for year-round community use in the often rainy Pacific Northwest.
The project prioritized occupant health by avoiding materials containing substances on the Living Building Challenge Red List, a collection of chemicals known to cause harm to people and the environment. Avoiding these materials was one of the team’s most significant project challenges, which meant limiting the materials palette and prioritizing natural products like mass timber for structural elements and wool textiles for the interiors.
Was a chemicals of concern list or other third-party framework used to inform material selection? If so, how?
Yes, the Living Building Challenge Red List was used. At the outset of design, the team developed a proactive process to identify safer materials, review products against the Red List, and minimize the number of overall materials in the project and, therefore, the amount of required product vetting. A materials review team used the Red2Green materials vetting database to review every project product against the Red List throughout design and construction. The team also implemented a process whereby all materials coming onto the site had to be checked in and approved prior to delivery.
How did the project advocate for greater transparency in building material supply chains?
As part of material Red List vetting, the project team contacted nearly 400 manufacturers to understand material ingredients and health impacts and advocate for greater transparency and healthy material ingredients when compliant materials were not available. The project affected several changes within the materials market, including working with manufacturers to perform testing and invest in new Red List–free materials. Several suppliers shared that the project inspired them to pursue Declare labels, which better position their manufactured goods in a healthy materials economy.
Metrics
65% of the regularly occupied area is daylit (sDA 300/50%)
0% of the regularly occupied area is compliant with glare criteria (ASE 1000, 250)
100% of the regularly occupied area has quality views
Is there occupant control? Yes, in 5 out of 6 categories
Is CO2 measured? Yes, 900 ppm is the design goal for maximum CO2
Please explain if a metric requires additional interpretive information.
Natural ventilation clarification: Levels 2–5 utilize natural ventilation through automatic and manual operable windows when outdoor conditions are favorable. Mechanical ventilation is still provided and reacts to CO2 levels. The natural ventilation controls allow spaces to be passively cooled, increase outside air to occupants, and provide biophilic qualities to the spaces.
Designing a 500-year building meant selecting inherently resilient and low-carbon structural materials. The team developed a strategy to minimize the amount of overall materials needed for the project. Eliminating finish materials as much as possible, utilizing a standard materials palette, and using materials for multiple purposes were all key to this goal. The team also prioritized local materials, including timber and finish carpentry and façade masonry. Vetting project materials against the Living Building Challenge Red List also ensured the team avoided many unintended impacts of common building products like vinyl on fenceline communities.
Interior components celebrate the aesthetic and structural value of mass timber. Exposed cross-laminated timber ceilings, glulam columns and beams, and salvaged wood throughout the project nod to Oregon’s timber industry. The third-floor reception desk and end tables are made from four maple trees that were felled on-site during construction.
Glazing was another notable material decision. The team initially designed for triple-paned windows on the office levels for energy and system-sizing reductions but discovered that double-paned windows with fiberglass frames essentially achieved the same performance with lower associated embodied emissions, so the change was made.
Did embodied carbon considerations inform the design? How?
Concrete, steel, and wood structures were all considered early in design. An embodied carbon analysis revealed that the wood structure had lower embodied carbon than both the concrete and steel structures. From a cradle-to-construction perspective, the wood building (including the entire core and shell) has 40% lower embodied emissions than the steel structure. A wood structure was ultimately selected as it reduced the carbon footprint of the building and dramatically improved the space’s biophilic nature without sacrificing building performance.
Did the idea of circularity/circular economy inform the design? How?
The project achieves a high level of material and economic efficiency by salvaging several items, many from the previous workspace of the primary tenant, including large ceiling fans, metal storage lockers, wooden cubbies, sit-stand desks, cabinet hardware, tables, chairs, and equipment that includes paper shredders, refrigerators, and a kegerator. Reclaimed wood is used not only in feature walls and the lobby ceiling but also for the building’s third-floor reception desk and end tables, which were built from maple trees felled on-site during construction. Cabinetry is made from a product composed of discarded construction wood waste.
Describe any special steps taken during design/construction to make disassembly, deconstruction, or reuse easier at the building's end of life.
Early in the project, the team crafted a materials waste reduction plan that grew to encompass design strategies, on-site construction waste recycling and reclamation (achieving 98.2% landfill diversion), ongoing operations, and material end-of-life. The building’s 500-year life—with the highest category seismic performance, flexible floor plates, and massing that maximizes height and allowable area in its historic district location—will ensure its future adaptability and utility.
Metrics
0% of floor area was reused or adapted from existing buildings
Was embodied carbon modeled? Yes
36.2 Predicted embodied carbon intensity (kgCO2e/sf)
100% of the installed wood is FSC certified
The PAE Living Building is inherently resilient and intended to be a lasting community asset. During construction alone, the building experienced ice storms, hazardous wildfire smoke, and a global pandemic, all very real reminders that climate change effects are happening now and the design must protect the building and its occupants.
Designed to meet Category IV structural resistance design criteria, the same level used for hospitals and fire stations, the building will be reusable after a Cascadia subduction event earthquake. The higher level of structural resilience reduces the potential swaying, diminishing the risk to other elements of the building, including the envelope. Its location within the 500-year flood zone considers that while water could reach the building’s first floor in a dire flood, the damage would be repairable and would not undermine the building’s foundation. Additionally, the structure can operate disconnected from the grid for up to 100 days during summer months, and the space has been offered for city of Portland use in the event of disaster.
The flexible floorplate anticipates future uses and can be modified to support future occupants with minimal interventions.
In what ways does the design anticipate climate change over the life of the building?
The building is designed beyond current code and its net zero energy and net zero water design and operations considers the very real possibility of future energy brownouts and blackouts as well as diminishing clean water. The building’s location in the Cascadia subduction zone is also accounted for with a seismic-resilient design. Its location within the 500-year flood zone considers that while water could reach the first floor, the damage would be repairable and would not undermine the building’s foundation.
How does the design anticipate restoring or adapting function in the face of stress or shock, such as natural disasters, blackouts, etc.?
The building was designed to meet Category IV structural resistance design criteria, the same level required by hospitals and fire stations, resulting in a structure that will be reusable after a Cascadia subduction event earthquake. This higher level of structural resilience reduces the potential swaying, diminishing the risk to other elements of the building, including the envelope.
Metrics
Was research conducted on likely hazards? Yes, on 7 out of 10 categories
Can the building be used as a safe harbor to support a community during a crisis? Yes
Passive Functionality: Partial backup power
How many hours can the building function through passive survivability? 2,400
Building design lifespan: 500 years
Was the building designed for disassembly? Partially
Please explain if a metric requires additional interpretive information.
The building is its own water system, with all potable and non-potable water collected from rainwater and overflow held in a 71,000-gallon underground cistern, which utilizes building foundation walls for its enclosure. The building can operate in a low-energy mode completely disconnected from the grid for at least a week. In addition, the building can operate for approximately 100 days in the summer without utility power.
The project was made possible in part due to the trust, experience, and knowledge that project team members gained working together on previous projects, including some of the most ambitious and sustainable structures of the past several decades.
One of the goals was to demonstrate what’s possible at the highest levels of sustainable design and inspire change. The building delivers on this goal via its revealed energy and water systems, a transparent materials palette, and interior spaces that are full of natural light and fresh air.
Over the past two years, more than 3,300 people from around the world have toured the building. They include members of the public, trade professionals, policymakers, nonprofits, and local student groups seeking to learn more about its construction and operations. Interpretive materials found throughout the structure help explain its functional areas and detail its features. QR codes link to explanatory information housed online, including the building’s energy use and generation data.
The team has also been extremely forthcoming in sharing lessons learned—both good and bad—through more than 50 media stories, dozens of conference engagements, and academic case studies in partnership with architecture and engineering schools around the U.S.
What lessons learned through this project have been used to improve subsequent projects?
Among the critical lessons learned that will be applied to future projects are the thermal and life cycle analysis benefits of fiberglass frames and the integration of structural mass timber systems. Battery electrical energy storage commissioning has proved invaluable in understanding the setup and operation of these systems for this and future projects. Additionally, the team has found vacuum flush toilets are effective and problem-free, saving about 90% water use for flushing. More challenging lessons have persisted with the greywater system and composter bug management.
If a post-occupancy evaluation was conducted, describe the process and outcomes.
A formal post-occupancy survey will commence in late 2023 as part of the project’s Living Building Challenge certification. Additionally, the team is working with students at Portland State University who will start in January 2024.
If a post-occupancy performance testing was conducted, describe the process and outcomes.
The team conducted post-occupancy performance testing for indoor air quality (IAQ). All spaces were compliant with ILFI IAQ standards prior to occupancy, and all but three building locations—lobby, a new tenant space, and a conference room—passed post-occupancy. Additional testing is pending following a ventilation flushing of the building.
If energy and/or water modeling was performed, describe any differences between predicted and measured use.
Data collected shows the building is performing as intended. During a 12-month period ending August 2023, the project generated 306,300 kWh and used only 281,600 kWh, creating 8.7% more energy than the building used. Tracking to meet Living Building Challenge compliance shows that the water and waste systems are also meeting net zero goals, and the urine capture system is currently sending fertilizer product to the market.
Metrics
Commissioning: Yes, Basic, Enhanced, On-goinh
Post Occupancy Engagement: Yes, in 7 out of 7 strategies
Transparency: Did the team share lessons of the project: Yes, in 10 out of 10 strategies
Who has access to performance feedback: All occupants
Please explain if a metric requires additional interpretive information.
A full year's energy and water data was just finalized and will be presented and published. However, other post-occupancy data, including building utilization, embodied carbon, and early updates on energy and water, have been published and/or presented to public.
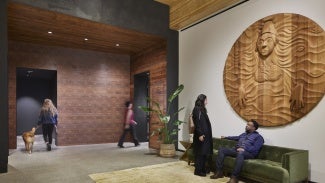
Explore additional images, detailed drawings, and diagrams for a visual narrative of architectural innovation integrating exemplary performance with a compelling design.
Project team & jury
Architect: ZGF Architects
Developer: Edlen & Co.
Contractor: Walsh Construction Co.
MEP Engineers and Technology Design: PAE
Lighting Design: LUMA
Structural and Civil Engineer: KPFF
Landowner: Downtown Development Group
Water Treatment (Rainwater and Composting): Biohabitats
Red List Materials Research: Brightworks Sustainability, Integrated Eco Strategy
Real Estate Partner: Apex Real Estate Partners
Building Envelope Consultant: RDH
Land Investment: Downtown Development Group (DDG)
Nadine Saint-Louis, AIA, Chair, McHarry Associates, Miami
Yu-Ngok Lo, FAIA, YNL Architects, Culver City, Calif.
Jack Rusk, Assoc. AIA, EHDD, San Francisco
Eddy Santosa, AIA, Mott MacDonald, Los Angeles
The COTE® Top Ten Award is the industry’s best-known award program for sustainable design excellence.
Explore projects setting the standard in design and sustainability, presented by the Committee on the Environment.