ROI: Designing for reduced embodied carbon
Architects play a pivotal role in reducing embodied carbon—a significant contributor to global annual emissions—within the built environment to address environmental concerns and reach decarbonization goals.
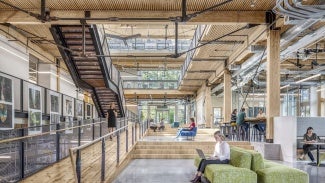
Embodied carbon environmental impact
The architecture profession can lead the way in going beyond operational carbon, the emissions associated with the energy used to operate the buildings, through addressing embodied carbon within their projects. Embodied carbon refers to the greenhouse gas emissions that are associated with materials and construction processes over the entire life cycle of a building.
Currently, the building industry generates almost 40% of annual CO2 emissions, illustrating that if significant reductions are taken, this industry can be a key leader in reaching decarbonization targets. Embodied carbon alone accounts for 11% of global annual emissions and is connected to issues of public health and equity. It is imperative that embodied carbon becomes a focus of emission reductions within the industry.
For more resources on embodied carbon, please see AIA's zero-carbon page.
Literature review completed by University of Washington’s Integrated Design Lab for AIA in 2020.
A building’s structure is one of the largest contributors to embodied carbon and capital cost; choosing efficient structural systems can significantly reduce both.1
Key efficient design talking points:
- A case study of an 18-story building showed that compared to a conventional reinforced concrete building, a reinforced concrete structure with a post-tensioned floor reduced embodied carbon and construction costs by 10% and 8%, respectively. The same study found that a completely mass timber building reduces embodied carbon by 26% and construction costs by 5%.*1
- Mechanical systems have a significant impact on total embodied carbon over the lifespan of a building project. *2 Incorporating passive design strategies reduces the size of the mechanical system, decreasing embodied carbon and initial first cost, and reduces operational expenses due to load reduction.*3
- Efficient space planning reduces the area of a building and the necessary materials, which also reduces embodied carbon and upfront costs.*4
- Minimizing earthwork and construction optimization strategies, such as minimizing idle truck and pump time and minimizing on-site transportation by optimizing the layout of a construction site, can reduce costs and minimize embodied carbon of construction.*5
- As building materials and systems become increasingly expensive in the future, designing for disassembly adds more value to buildings over time, as owners can salvage or sell building materials at the end of life, saving embodied carbon and providing a revenue stream.*5,6
- One study of a precast concrete, 14-story building showed that designing for disassembly reduced deconstruction costs by up to 9.4% and reduced carbon emissions by up to 40% during the deconstruction process.*6
References
- Robati, M., Oldfield, P., Nezhad, A., Carmichael, D., & Kuru, A. "Carbon value engineering: A framework for integrating embodied carbon and cost reduction strategies in building design." Building and Environment. 2021.
- Rodriguez, B., Huang, M., Lee, H., Simonen, K., & Ditto, J. "Mechanical, electrical, plumbing and tenant improvements over the building lifetime: Estimating material quantities and embodied carbon for climate change mitigation." Energy and Buildings. 2020.
- Hawkins, D., & Mumovic, D. "Evaluation of life cycle carbon impacts for higher education building redevelopment: A multiple case study approach." Energy and Buildings. 2017.
- Cousins, F., Broyles Yost, T., & Bender, G. "Think circular–Reducing embodied carbon through materials selection. MRS Energy & Sustainability." MRS Energy & Sustainability. 2018.
- Akbarnezhad, A., & Xiao, J. "Estimation and Minimization of Embodied Carbon of Buildings: A Review." Buildings. 2017.
- Akbarnezhad, A., Ong, K., & Chandra, L. "Economic and environmental assessment of deconstruction strategies using building information modeling." Automation in Construction. 2012.
Low embodied carbon substitutes in material specification can reduce embodied carbon with no cost premium and even cost savings.*1
Key material selection talking points:
- A review of case studies showed that substituting materials with lower embodied carbon alternatives saves 19–46% of embodied carbon at a cost premium of less than 1%.*1
- Substituting cement with slag, fly ash, or other pozzolanic or lime-based materials can reduce embodied carbon by 14–33% at no cost or even a cost reduction.*1
- Selecting low embodied carbon insulation materials, such as using polyiso or mineral wool batt instead of XPS, can reduce embodied carbon by 16% at no cost premium.*1
- Applying life cycle assessment (LCA) design frameworks early in the design phase optimizes the use of building elements and materials, which has the potential to reduce material volume and operational carbon emissions, reducing the associated up-front and long-term costs.*2
- One study of an 18-story apartment building found that substituting high embodied carbon materials with low-carbon alternatives led to a 74% decrease in embodied energy and a 30% cost reduction.*3
- Choosing higher-quality materials can reduce the need for repairs and maintenance, reducing the embodied carbon associated with repairs.*4
- A study comparing material selections in a single-family home found that using durable materials reduces embodied carbon up to 30% compared to standard construction.*5
- Recycling and upcycling materials can be cost effective and save embodied carbon. Using durable materials yields up to 30% lower embodied carbon compared to the reference, whereas a design for adaptability results in 17% lower embodied carbon.*5
References
- Jungclaus, M., Esau, R. Olgyay, V., & Rempher, A. "Reducing Embodied Carbon in Buildings: Low-Cost, High-Value Opportunities." Rocky Mountain Institute. 2021.
- Cang, Y., Luo, Z., Yang, L., & Han, B. "A new method for calculating the embodied carbon emissions from buildings in schematic design: Taking 'building element' as basic unit." Building and Environment. 2020.
- Manjunath, A., & Patil, N. "Effect of sustainable materials on embodied energy, carbon footprint and cost for a proposed conventional apartment." IOP Conference Series. Materials Science and Engineering. 2021.
- Brás, A., & Faria, P. "Effectiveness of mortars composition on the embodied carbon long-term impact." Energy and Buildings. 2017.
- Rasmussen, F., Birkved, M., & Birgisdóttir, H. "Low-carbon design strategies for new residential buildings - lessons from architectural practice." Architectural Engineering and Design Management. 2020.
Sustainable retrofits increase the asset value of a project over time while also reducing embodied carbon compared with demolishing and building new.*1
Key renovating and retrofitting talking points:
- Sustainable retrofits increase the asset value of a project over time while also reducing embodied carbon compared with demolishing and building new.*1
- For energy retrofits, performing an analysis of operational and embodied carbon optimization will reveal opportunities to reduce operational expenses while minimizing material investment.*2,3
- A 50–75% savings in embodied carbon is possible by repurposing an existing building.*4
- Designing for disassembly saves resources and time when retrofitting and repairing, reducing the renovation costs considerably.*5
- Floors in high-rise office buildings regularly undergo new tenant build-outs, so designing for easy fabrication and de-fabrication will help save costs and embodied carbon in high-turnover spaces.*6
References
- Menassa, C. "Evaluating sustainable retrofits in existing buildings under uncertainty." Energy and Buildings. 2011.
- Shadram, F., Bhattacharjee, S., Lidelöw, S., Mukkavaara, J., & Olofsson, T. "Exploring the trade-off in life cycle energy of building retrofit through optimization." Applied Energy. 2020.
- Shirazi, A., & Ashuri, B. "Embodied Life Cycle Assessment (LCA) comparison of residential building retrofit measures in Atlanta." Building and Environment. 2020.
- Jungclaus, M., Esau, R. Olgyay, V., & Rempher, A. "Reducing Embodied Carbon in Buildings: Low-Cost, High-Value Opportunities." Rocky Mountain Institute. 2021.
- Akbarnezhad, A., Ong, K., & Chandra, L. "Economic and environmental assessment of deconstruction strategies using building information modeling." Automation in Construction. 2012.
- Forsythe, P., & Wilkinson, S. "Measuring office fit-out changes to determine recurring embodied energy in building life cycle assessment." Facilities. 2015.
Key future-proofing and labeling talking points:
- Reducing embodied carbon in a project can help projects achieve green building certifications from LEED v4, Zero Carbon, the Living Building Challenge, and other widely recognized certifications.*1
- Future building codes and policies will likely require reduced embodied carbon of buildings through a carbon tax, building code requirements, and procurement policies. Developers and architects accustomed to building low embodied carbon buildings will be better prepared for these policy changes.*1
- Green labeling can increase the asset value of a project. See page: ROI: Increasing asset values: green labeling
References
How to use these talking points
These talking points are intended for use in your conversations with clients, potential clients, civic leaders, vendors, contractors, and other architects. This helps demonstrate that architects are trusted partners in strengthening society, designing solutions, and transforming communities.
This is one chapter in AIA’s series ROI of High-Performance Design. Access the full resource below.
Explore the next chapter in ROI of High-Performance Design.