Design for Resources—Framework for Design Excellence
Good design depends on informed material and resource selection—balancing priorities to achieve durable, safe, and healthy projects with an equitable, sustainable supply chain to minimize possible negative impacts on the planet.
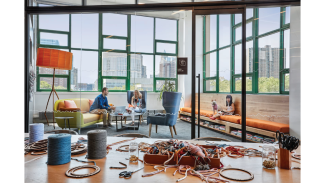
- What factors or priorities will be considered in making material selection decisions?
- How are materials and products selected and designed to reduce embodied carbon and environmental impacts while enhancing building performance?
- How can material selection reduce hazards and support equitable labor practices in the supply chain?
- How does the project promote zero waste throughout its life cycle?
- How does the project celebrate local materials and craft?
- How long will the project last, and how does that affect your material?
Focus topics
- Material sourcing
- Healthier materials
- Embodied carbon
- Construction, deconstruction, & demolition
- Zero waste operations
- Circular economy
Design for Resources toolkit
If you can do only one (or a few) thing(s):
- ZERO CARBON: Select products that reduce carbon emissions and sequester more carbon emissions than are emitted during the construction process. Consider the materials’ carbon footprint from cradle to cradle.
- RESILIENT: Consider the durability of materials to withstand anticipated shocks and stresses.
- EQUITABLE: Consider the health of communities where resources are extracted, harvested, manufactured, and disposed. Select products from manufacturers that secure human rights in their own operations, positively impacting their workers and the communities where they operate. Demand product transparency.
- HEALTHY: Simplify the building materials palette to reduce the potential for chemicals of concern and prioritize healthier materials. Select products that seek to eliminate the use of hazardous substances.
Material sourcing
Material selection is perhaps the most clearly defined responsibility of an architect, and yet the goals for sustainable and resilient materials are varied and occasionally mutually exclusive. Traditionally, materials were selected for aesthetics, durability, availability, and cost. First-generation sustainable goals sought to reduce waste, favor regional materials, and improve indoor air quality. Second-generation goals added more criteria: to reduce embodied carbon emissions, provide ingredient transparency, and avoid chemicals of concern. Architects are working closely with manufacturers to encourage materials and products that enhance human health, climate health, ecosystem health, and social equity within a circular economy (see the AIA Materials Pledge).
Actions:
- Source materials that support and regenerate the natural air, water, and biological cycles of life through thoughtful supply chain management and restorative company practices.
- Prefer manufacturers that embrace transparency and secure human rights in their own operations and supply chains and seek out supply chains that are not involved in modern slavery and provide positive impacts for their workers and the communities where they operate. Living Product Challenge-certified products are great examples of products that embody these ideals. Specify materials that are extracted and/or manufactured in ways that do not degrade ecosystem and community health in addition to having high recycled content. Grace Farms Design For Freedom Toolkit can help design professionals implement ethical, forced-labor-free materials sourcing strategies into their practices.
- Prefer manufacturers with a high level of product transparency. If information does not exist, ask and work with manufacturers to produce and provide Environmental Product Declarations (EPDs), Health Product Declarations (HPDs), and Declare labels. Consider products with an extended producer responsibility, especially for FF&E (furniture, fixtures, and equipment), which have a shorter service life. This includes the circular economy model where manufacturers provide products as a service or have a takeback program.
- Think locally and regionally. Develop a regional materials palette based on what is available locally, especially for heavier materials. Increase your radius to meet product criteria. When possible, design with reclaimed/salvaged materials such as bricks or lumber, and reclaimed components such as furniture systems, raised floors, and commercial doors. Work with your team of consultants to ensure best use of the material from both a functional and end-of-use perspective.
- Responsible material sourcing requires time and commitment from the design team. Incorporate product research, specification, review, and tracking in the project budget to ensure requirements for tracking materials declarations, requirements that increase the use of materials and surplus, and material best practices are followed from specification to contractor procurement.
Healthier materials
The manufacture, installation, use, and end-of-life plan of building materials have long-term and significant impacts on human and environmental health. Choose healthier materials that support and foster life throughout multiple use cycles and seek to eliminate the use of substances that are hazardous.
Actions:
- Set material health goals for the project and make these known to the team. Require that the contractor document progress toward the goals during monthly review for payment. Establish a clearly defined “Do not substitute” list and ask the contractor to keep records or get approval for any additional products used in the project.
- Exclude chemicals of concern. Use an established list, such as the ILFI Living Building Challenge Red List to help make decisions on what materials and products to select, and that have ingredient transparency data such as the “Declare” labels or Cradle to Cradle Certified products. Set ingredient disclosure documents, such as Health Product Declarations (HPDs), as a minimum threshold. Where third-party-verified material ingredient documentation doesn't exist, ask for it (see Material Sourcing section). Begin by selecting just one chemical of concern to avoid in a project (such as vinyl/PVC, flame retardants, or formaldehyde), then improve from there. Use SixClasses.org as a reference to choose chemicals that are most appropriate to avoid given the occupants of your building.
- Focus on products to which people will be most exposed—within the waterproofing membrane, for example, or within the interior finishes.
- At the firm level, choose one or a few chemicals of concern to eliminate in the firm’s standard specifications or a project’s materials. Start with your firm’s most commonly used materials and provide good, better, and best options.
- Consider the possible impacts of a disaster on materials. Will flooding cause chemicals to leach from wallboard? Will an earthquake release hazardous materials that have been encapsulated? Mitigate these potential sources of contamination.
Embodied carbon
In the next 30 years, 90% of all new building emissions will come from building materials as operational carbon emission values fall due to stringent energy code requirements, the energy grid adding more renewable energy, and innovations leading to greater energy efficiency in buildings. Extending the life of an existing building and utilizing low-carbon products will have a meaningful impact on reducing carbon emissions in the building sector.
Actions:
- Building reuse, space efficiency, building longevity and adaptability, and structural optimization save material resources and are the first approaches to consider reducing embodied carbon. Determine the anticipated service life for the building in its location. Select a palette of materials that align with the service life or can be disassembled and reused after the building as a whole is no longer viable. A whole building life cycle assessment (LCA) is like an energy model for a project’s materials. Performing an LCA will help identify project-specific challenges, global warming potential of materials, and targets for carbon emissions reduction. Links to tools for preparing a LCA are listed below.
- Set embodied carbon targets for high-impact materials, such as concrete, asphalt, wood, steel, flat glass, and insulation, on all projects. For tenant improvement (TI) projects, focus on carpet, gypsum board, and FF&E, and consider product lifespan, reuse, and takeback. Carbon Smart Materials Palette is a good resource during early design for information on strategies and alternative materials.
- The embodied energy of wood varies significantly based on forestry practices. Choose reclaimed and salvaged wood, where possible, and avoid wood from rainforests or old-growth forests. Wood should be FSC-certified, which must be verified by checking the Forest Management Certificate number on the wood invoice. Other sustainable sources may also be available locally (e.g., black locust or diseased ash from ecological restoration projects and wood from tree pruning services or from smaller managed forests following Slow Wood Criteria). Use smaller and variable dimensions of wood where possible. For decking, 100% recycled plastic lumber is a durable alternative.
- Prefer recycled or biobased materials from waste agricultural products such as straw and ensure that other products are grown and harvested sustainably; good choices include linoleum, strawboard, and hempcrete. Biobased materials can be perpetually renewed, but available land is limited, so old-growth forests are clear-cut for tree plantations, and valuable agricultural land is farmed for ethanol and bioplastics.
- Reduce the Portland cement content in concrete. Good strategies include specifying concrete with a high supplementary cementitious material (SCM) content (good choices include glass and natural pozzolans, and Portland lime cement), and extending curing times from 28 days to 56 days or longer.
- Specify steel from electric arc furnaces, which also ensures a high recycled content.
- Choose insulation with low embodied carbon; good choices include cellulose or mineral wool. Minimize use of spray foam, and, where used, specify hydrofluoroolefin (HFO) rather than hydrofluorocarbon (HFC) blowing agents.
Construction, deconstruction, & demolition
Most building materials are made from finite virgin resources and end up in a landfill or incinerator. Design and specify for a circular economy by using salvaged and recycled materials, reducing waste generated during construction, and facilitating future reuse of building components and materials.
Actions:
- Work with the contractor to estimate the quantity of waste to be generated during construction and identify measures to reduce waste, such as takeback for surplus materials, just-in-time ordering, reducing packaging, allowing offcuts to be reused, and other lean construction strategies, including balancing cut and fill to allow reuse of excavation materials.
- Set goals for deconstruction, demolition, and construction waste diversion, and require waste tracking by the contractor during demolition and construction. Require the contractor to use Recycling Certification Institute (RCI)–certified facilities, if they exist locally, to ensure accurately documented diversion rates.
- Specify separation on-site for easily damaged recyclable waste, such as gypsum board, ceiling, and carpet tiles. Reduce construction errors through BIM models, careful coordination, and prefabricated off-site construction.
- Where there is an existing building on-site, assess if full or partial building reuse is an option. Conduct a vulnerability assessment to determine if observed or foreseeable hazards may affect the future service life. Perform a survey in the early design phase to assess opportunities for deconstruction and reuse of materials in the new project or elsewhere. Write specifications to allow substitutions of approved reclaimed components and materials.
- Design for spatial flexibility to allow the building to be adapted for different uses and minimize waste created in future renovations.
- Design for disassembly of building components and materials through reversible attachments. Ensure that materials can be easily isolated and removed during renovations, for example, by using carpet tiles that are secured to each other rather than glued to the floor.
- Consider developing a material information database, or “material passport,” to assess the value of materials in the building and to facilitate their future reuse.
Zero waste operations
Waste created in daily building operations, especially food and single-use packaging waste, has major environmental impacts, so buildings should be designed to facilitate zero waste operations. Zero Waste Design Guidelines is a comprehensive resource of design strategies to reduce operational waste.
Actions:
- Develop a waste management plan, with input from building management, that estimates quantities of each waste type and identifies how and where they are collected, moved, stored, and set out for pickup. Provide sufficient area for easy segregation, movement, and storage of all discarded materials, including, as applicable, metals, glass, plastics, cartons, paper, cardboard, organic waste (food scraps, compostable packaging, and landscape waste), bulk waste, electronic waste, light bulbs, plastic film, and textiles. To increase accurate sorting and recycling, design central waste and recycling stations rather than individual bins that accumulate unsorted waste. Ensure clear, consistent signage and visual cues at waste segregation and storage locations throughout the building.
- Provide sufficient dishwashers and storage for use of durable tableware in food service spaces and water fountains and bottle-fillers to reduce single-use packaging waste. Consider equipment in food service spaces to dewater food waste, which can be up to 90% water. This reduces odors, pests, and the volume of waste. In projects with landscaped areas, consider composting equipment to allow on-site.
- To incentivize waste reductions, materials need to be “metered” and “sub-metered” just like electricity or water. In buildings with multiple tenants, provide a shared waste storage room that allows for tracking waste by type. This saves overall space and allows the provision of shared waste equipment.
- Consider equipment to reduce the volume of waste, such as cardboard balers or compactors, which decrease storage space requirements and truck trips.
Circular economy
Architects and designers have become accustomed to designing new buildings with limited lifespans instead of capitalizing on the significant investment and reusing the buildings or building components for generations. This status quo is inefficient, wasteful, and squanders the earth’s finite natural resources. Demolition activities are significant contributors to global waste. Teams are encouraged to consider the value of reusing existing building stock over new construction. Renovation and new construction methodologies and specifications must evolve to be based on product modules (to eliminate cutoff waste), design for disassembly, and reuse. Recycled and recyclable buildings and building materials are key components of a circular economy.
Favor materials with high post-consumer recycled content over materials with pre-consumer recycled content, although both are acceptable. (Post-consumer recycled content comes from materials already in a product that otherwise would have ended up in a landfill. Pre-consumer content comes from materials that would have been discarded in manufacturing processes and would have otherwise ended up in a landfill, such as offcuts and rejects, but are repurposed for use in products.)
When favoring products that can be recycled into like products rather than be downcycled into a lesser product, consider that many products are difficult to recycle because they contain materials that are difficult to separate and/or are different types of “nutrients.” A material can be a technological nutrient that can be reprocessed into a like material or a biological nutrient that could feed a natural cycle. For example, most metals and some plastics, being technological nutrients, can be reconstituted into a new product with similar characteristics. However, wood pulp, which is a biological nutrient, can often be downcycled into something not quite as substantial as the original product, or can be composted into soil (unless the binders used in the original product are toxic). Some building materials are composite products with unlike materials bound in layers or blended. For example, some blended products contain wood fibers (a biological nutrient) mixed with either cementitious materials or plastic (technological nutrients) and are generally not recyclable.
Actions:
- Support building design and product selections that contribute to a circular economy by reusing and improving existing buildings, designing for resiliency, adaptability, disassembly, and reuse; aspiring to a zero-waste goal for buildings; and specifying products that contain recycled content and/or products that can be recycled.
- Renovate, retrofit, and reuse. Advocate for teams and clients to reuse and renovate existing building stock and reuse salvaged building materials. Take advantage of the strong financial and carbon reduction arguments.
- Design new buildings with a plan for future ease of disassembly or with a strategy for how the building may be reused in the future. Explore strategies that can make disassembly and reuse easier.
- Reduce construction waste.
- Consider modular design and off-site construction to increase efficiency in the entire construction process. Select building materials and furnishings with high recycled content and with the ability to be recycled into an equal quality product (rather than downcycled into a lesser quality product). Additionally, select materials and furnishings from manufacturers with active product leasing or takeback programs.
- Research which manufacturers have active take-back programs to reclaim the value of the original materials. This is most common in carpeting, acoustical ceiling materials, and furnishings, although take back programs in other product categories are becoming more common.
- Prioritize the use of natural building materials. Natural materials like wood and stone are the first options for low-impact materials (especially if they meet sustainability certifications such as FSC for wood and The Natural Stone Sustainability Standard – ANSI/NSC 373 for stone).
- Co-released by AIA and the National Trust for Historic Preservation, Building Reuse: A Proven Climate and Economic Strategy is a brief resource that overviews the importance of building reuse to reduce total carbon emissions and create new jobs through historic rehabilitation.
- This ILFI Red List of chemicals of concern provides a variety of frameworks for keeping dangerous chemicals out of the built environment.
- You can use Six Classes webinars as a reference to choose a class of chemicals that are most appropriate to avoid for the occupants of your building.
- mindfulMATERIALS (mM) and UL SPOT are extensive searchable databases for sustainable project materials. Search for products with HPDs, EPDs, declare labels, etc.
- The Carbon Leadership Forum has introductions to Embodied Carbon Policy, a Life-Cycle.
- Carbon Smart Materials Palette contains an attribute-based approach to embodied carbon reductions in the built environment. It identifies key attributes that contribute to a material’s embodied carbon impact, and offers guidelines and options for emissions reductions, low/no carbon material selections, and specifications.
- Design Data Exchange (DDx) now has input options to track embodied carbon along with operational carbon emissions.
- Tally, Athena, One Click LCA, and BHoM tool are LCA software available for use with BIM models.
- Use the Embodied Carbon in Construction Calculator (EC3) to focus on the upfront (Stage A1–A3) supply chain emissions of construction materials and find and optimize products.
- Parsons’ Healthy Material Lab materials collections, products, spec guidance, and educational resources.
- BuildingGreen’s The Great Eight: High-Impact Material Choices for Green Building shows what to specify and what to avoid.
- AIA has guides on Renovate, Retrofit, Reuse to help architects design for deconstruction or reuse an existing structure, as well as design for adaptability in a new construction project.
- AIA New York's Zero Waste Design Guidelines addresses how to design a building for zero waste operations and circular building materials.
Design excellence case studies
Explore four COTE® Top Ten award recipients demonstrating successful resource design:
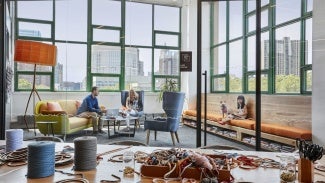
Etsy Headquarters
Brooklyn, New York | Gensler
An adaptive reuse project that focused on using salvaged materials and avoiding finishes wherever possible to reduce the projects’ embodied energy. Excess building materials were used by other nearby projects. USGBC TRUE Zero Waste Platinum–certified for zero waste operations.
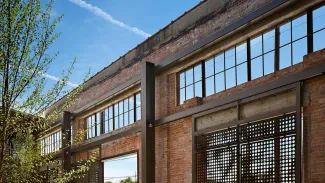
Hughes Warehouse Adaptive Reuse
San Antonio, Texas | Overland Partners
This adaptive reuse restored existing structures and finishes and reused materials from partial demolition in other areas of the building (wood joists for stairs, concrete for pavers). Furniture from the previous office was remilled and reassembled. The modular wall system allows for future flexibility.
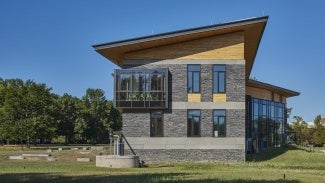
R.W. Kern Center
Amherst, Massachusetts | Bruner/Cott & Associates
Wood as a primary structural material reduces embodied carbon footprint. Local materials (stone for cladding, using trees from the site for tables, salvaged oak planks) play a large role. End-of-life impacts were key to material decisions (cellulose insulation is recyclable; bolted connections of the structure allow for disassembly; simplicity of material palette eases sorting during disassembly).
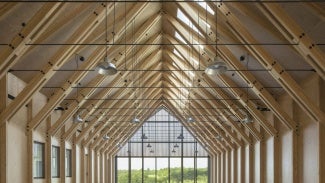
Tashjian Bee and Pollinator Discovery Center
Minneapolis, Minnesota | MSR Design
The Discovery Center project was designed for disassembly with wood panels and trusses that were unfinished and mechanically fastened. The primary finish material (accoya) is a C2C gold modified-timber product. Charred finish avoids exterior varnish that is harmful to bees.
Learn how the framework inspires and provides a toolkit for sustainable, resilient, and inclusive design.
Explore the next chapter of the Framework for Design Excellence—Design for Change.
This publication is designed to provide accurate and authoritative information in regard to the subject matter covered. It is published and distributed with the understanding that the publisher is not engaged in rendering professional services. If professional advice or other expert assistance is required, the services of a competent professional person should be sought.
AIA does not sponsor or endorse any enterprise, whether public or private, operated for profit. Further, no AIA officer, director, committee member, or employee, or any of its component organizations in his or her official capacity, is permitted to approve, sponsor, endorse, or do anything that may be deemed or construed to be an approval, sponsorship, or endorsement of any material of construction or any method or manner of handling, using, distributing, or dealing in any material or product.
If you have any questions or feedback regarding the Framework for Design Excellence, please let us know.