Harvard University Science and Engineering Complex
The award-winning sustainable design of the Harvard University Science and Engineering Complex helps shift the typology toward environmental stewardship to create one of the healthiest and most energy-efficient laboratory buildings in the world.
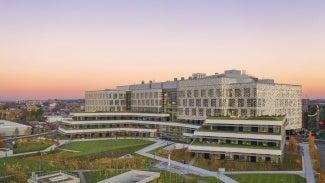
Project highlights: Harvard University Science and Engineering Complex
- Architecture Firm: Behnisch Architekten
- Owner: Harvard University
- Location: Boston
- Project site: Brownfield
- Building program type(s): Education – College/University (campus-level), Laboratory
Among the healthiest and most energy-efficient laboratory buildings in the world, Harvard’s Science and Engineering Complex (SEC) helps shift the typology toward environmental stewardship. It sets a new standard for Harvard and highlights its mission to shape a more sustainable university community and planet. Designed to reflect the leading research taking place inside, the complex also connects users to one another in the spirit of collaboration. It was built just over the bridge from Harvard’s Cambridge campus in Lower Allston, one of 23 neighborhoods that make up the City of Boston. The goal was to create a new sustainably built home for the Harvard John A. Paulson School of Engineering and Applied Sciences (SEAS) where a robust culture of collaboration and interdisciplinary work could be fostered. The SEC site is also a connector that links the neighborhood and Boston’s park system.
AIA Framework for Design Excellence principles
Harvard’s Science and Engineering Complex (SEC) is one of the healthiest and most energy-efficient laboratory buildings in the world. Certified by two international sustainable building programs, the International Living Future Institute (Living Building Challenge Materials, Beauty, and Equity petals) and the U.S. Green Building Council (LEED Platinum), the SEC is a centerpiece of Harvard University’s mission to create a healthier, more sustainable campus, community, and planet.
Explore how the Harvard University Science and Engineering Complex plays a key role in connecting the Lower Allston neighborhood, in a safe, car-free manner, to the Greater Boston Greenbelt, Public Park system, and natural amenities in Fig. 1 Design for Integration.
The SEC, from its inception, was meant to be an agent for change by simultaneously reorienting the scientific research building typology toward ecological stewardship, setting a new standard for healthy buildings on Harvard University’s campus and fostering an environment of connection, collaboration, and community. While related, these challenges each required substantively rethinking the fundamentals of institutional research building design. Accomplishing this required an approach with both breadth and depth that balanced technical, anthropological, and ecological needs—one that involved examining researchers’ day-to-day activity patterns, defining new standards for health and safety across the campus, exhausting passive-design measures, employing ultra-high-efficiency technologies, and investigating over 5,600 individual building products and systems to minimize the use of harmful substances such as PFAs, chemical flame retardants, and PVC.
The resulting 544,000-square-foot building was designed to reflect the cutting-edge research that happens inside, all while connecting building occupants to each other and to the natural beauty and life of New England. Operable windows in all regularly occupied spaces bring fresh air into the building, floor plate dimensions are kept to the minimum to ensure quality daylighting throughout the facility, and generous vertical circulation in the form of open stairs, bridges, and ramps encourage occupants to move, to see and be seen, and to collaborate with colleagues. This is extended to the project’s ground level and outdoor spaces, where not only students and researchers but the local community and public are invited to visit, linger, interact with and observe the work within, and enjoy the generous regenerative outdoor spaces.
Like a living, breathing organism, the SEC relies on an integrated network of self-regulating systems that supplement the passive design methods. To enhance the building’s performance, its architects and engineers employed advanced solar shading strategies, adaptable ventilation methods, a high-performance heat recovery system, an energy-saving air cascade system, superior insulation, air-sealing techniques, triple glazing, and renewable energy.
The SEC marks a major step toward Harvard’s goal to be fossil fuel-free by 2050 and to reduce damage to human and ecosystem health. With the SEC, the design team and their partners have translated research into practice and transformed a typically highly energy-intensive building typology into one that meets and exceeds present-day energy targets. By joining forces with students, community members, local and global businesses, designers, and researchers, the team has motivated others to support the design of healthier and more responsible built environments at all levels. Together, we are transforming the definition of sustainable building to address climate, health, and equity for all.
The SEC is located at the edge of a small but vibrant community called Lower Allston, which is one of 23 neighborhoods that make up the City of Boston. Throughout the 20th century, the neighborhood was cut off from both the Charles River and greater Boston when it was enclosed by an industrial district and an interstate. Before construction, the land on which the SEC was built was a brownfield, the result of industrial and manufacturing operations. To restore the site, which was polluted by lead, cadmium, petroleum hydrocarbons, and volatile organic compounds, the project removed and properly disposed of over 150,000 tons of soil. The lush regenerative landscape that replaces it is open to the public and provides a pivotal link between Lower Allston residents and the Boston Public Parks system. It seeks to be a model for how to restore local ecologies and landscapes.
Design intent
Who does the project serve? Identify the stakeholders who are directly or indirectly impacted by the project.
The primary stakeholders are the residents of the Lower Allston neighborhood and the students, faculty, and staff of Harvard University. The site sits in the quiet neighborhood of Lower Allston, which is primarily composed of duplex and multifamily housing as well as small businesses. It is adjacent to the Allston branch library and the adjoined Library Park. The students and faculty of Harvard University that will use the educational and research program, and the staff that will support and maintain it, are the primary building occupants. However, the neighborhood is also affected due to its proximity.
Describe the stakeholder engagement process over the course of the project.
Stakeholder groups answered survey questions about their vision for the SEC and attended workshops during the design phase. Design and construction progress was shared with the community via an intranet site, community meetings, and emails. In addition to the main groups, smaller working groups were consulted as needed. For example, a group of bicycle commuters participated in studies related to bicycle parking and provided feedback about their preferred bike racks. The design team walked the building with representatives from Harvard University Disability Resources after construction was complete and made modifications to spaces, equipment, furniture, and signage based on their evaluation.
Identify project goals that support equitable communities and describe how those goals were developed.
The SEC is a living laboratory for world-class, interdisciplinary research, learning, and innovation. The first floor of the SEC was envisioned to be an extension of the urban realm and open to the public to observe “science on display” through a permeable floor plan, large areas of glazing at teaching labs, and classroom spaces. The ground floor was intentionally set at grade along Western Avenue to enhance the connection to the public realm and is transitioned to a higher elevation inside the building by universally accessible ramps in response to the future threat of sea-level rise.
Describe the project team's explorations or design strategies that respond to the above-stated goals.
The SEC is a model for a different kind of experience in the built environment—one that prioritizes comfort and well-being. Throughout the building, users will encounter a variety of serene, daylit, well-ventilated open spaces along with hundreds of trees and plants that improve air quality and bring the natural world inside, contributing to the building’s biophilic design.
Describe stories or evidence that demonstrate how the project successfully contributes toward more equitable communities.
Harvard developed an SEC Cooperation Agreement to support housing linkage, public realm improvements, workforce development, jobs linkages, education programs, partnerships, and maintenance for the adjacent library park. By 2021, over $23 million had been spent on these efforts. Addressing the Boston Residents Jobs Policy, the workforce for the project consisted of 27% Boston residents and 30% people of color. Turner Construction participated in the Building Pathways program, creating opportunities for low-income individuals in building trades. Sullivan & McLaughlin Companies (electrical and technologies) sponsored five Madison Park High School graduates into the Electricians Union, and they were placed directly on the SEC project.
Every community is unique, and every project has unique opportunities to respond to issues of equity and inclusion. Describe any exemplary practices or outcomes for this project.
Over half of the land, a former brownfield site and parking lot, was cleaned and converted into a green space that is open to the public. The public green has lawns for activities, regenerative zones to reintroduce healthy habitats, picnic tables, chairs, walking paths, and more. It is an asset to the neighborhood just as the building is an asset to the university. A protected greenway connects Lower Allston to the Charles River to the north via tree-lined, dedicated bike and walking paths, ensuring a safe connection to Boston’s natural landscapes. Multimodal connections to greater Boston are plentiful. There are bike racks, multiple covered bike shelters, protected bike lanes running both north-south and east-west, bus stops, and protected sidewalks. Sixty new trees were planted between the sidewalks and streets to help revive the local canopy.
As part of its commitment to addressing dangerous chemicals in building materials, the team leveraged the SEC to evaluate more than 6,000 products and educate, advocate, and partner with manufacturers to create a safer global supply chain. During the design and construction of this building, more than 1,200 companies disclosed the ingredients in their products and made this information publicly available. Many manufacturers reformulated their products to remove harmful chemicals.
In planning, building, and designing the SEC, Harvard made an effort to be as transparent and collaborative as possible with students, researchers, faculty, staff, the local community, the city of Boston, and the general public. Harvard conducted a needs assessment in 2008, surveying neighborhood residents. Residents shared interests in education, housing, multimodal transportation, public space, and sustainable development.
The SEC site was formerly a brownfield. The project restored the site by properly disposing of over 150,000 tons of contaminated soil and replacing it with a regenerative landscape.
The landscape was designed to increase biodiversity and plant health, reduce potable water use for irrigation, and provide healthy gathering spaces for the university and the surrounding community. The landscape is constructed such that wet meadow plant communities cleanse stormwater collected from the landscape and building roofs. The site extends the greenway, joining residential neighborhoods and public parks with university spaces and commercial development. It provides educational opportunities through visibility, demonstration, and quantifiable performance. It has been intentionally designed as an immersive teaching tool for the university, neighborhood, and other groups, making visible the landscape’s history, evolution, and performance.
Plant species were selected to improve the health of the site and the surrounding community. Locally sourced trees were chosen to help filter the air and increase the carbon sequestered on-site. The landscape fosters cohabitation between humans and pollinating species.
Design intent
How does the design minimize negative impacts on animals?
Site lighting was modeled to optimize fixture locations and lighting levels for adequate illumination and safety. LED fixtures were selected to minimize glare and provided downlight optics and reduce urban light pollution. The façade shading systems obscure reflections in glazing and horizontal surfaces for the shading panels, and shading wings were optimized to resist and prevent roosting.
How does the project support biodiversity and improve ecosystem services?
Rigorous research unearthed the site’s transformational history—and the history of the ecology that evolved with it. Using the research as a guide, adapted plant communities were developed that reference the site’s history. The wet meadow, urban savanna, and thicket communities support pollinators like butterflies, bees, and birds with blooming vegetation and sustenance that allows a richer campus and neighborhood ecology.
Metrics
0% of site area was vegetated (landscape or green roof) pre-development.
81.9% of the site area is vegetated (landscape or green roof) post-development.
There was a 81.9% increase in vegetated area, post-development.
60.6% of the vegetated areas are planted with native species.
The building is designed and constructed to minimize the discharge of stormwater off-site and to minimize the use of city water. This is accomplished by aggressive conservation and stormwater reuse within the facility and site boundaries. All stormwater falling on the site is collected, treated, and stored for reuse. Green roofs attenuate the stormwater flow and reduce discharge on an annual basis through evapo-transpiration. Runoff from roof and landscape areas flows into three site bioretention basins and constructed wetlands before draining into the six basement storage tanks with a total capacity of 78,000 gallons. Condensate from cooling coils is also collected and discharged directly into the tanks. The stored water is then treated and used to satisfy building requirements for toilet flushing, irrigation, RO/DI (lab pure water) makeup, humidification, and indirect evaporative cooling. RO/DI system reject water is combined with the reclaimed stormwater to serve the toilet flushing system. Excess water not used in the building is pumped back to the central heating and cooling plant for reuse. Only under exceptionally high rainfall is there overflow from the bioretention basins/tanks to below-grade infiltration galleries and then to the city stormwater system.
Explore the Harvard University Science and Engineering Complex’s Design for Water strategies, including storm-water management and water reuse strategies, in Fig. 2 Design for Water.
Design intent
Describe how the project's stormwater and potable water strategies contribute to site and community resilience.
The site is capable of handling 100% of stormwater on-site through a combination of landscape elements, bioretention basins, and stormwater tanks, which then feed various building water demands. The overall stormwater management system and reuse strategies ensure minimal runoff into the city stormwater system and Charles River. If runoff occurs during extreme precipitation events, the bioretention basins mechanically treat the water for solids and phosphorus.
Describe the quality of the water that runs off the site.
Precipitation events that exceed the two-year storm are directed to the drainage system around the SEC project, but only after going through the series of vegetated swales and bioretention systems. All stormwater that falls within the SEC site is treated prior to discharge into the city drainage system to reduce the TMDL phosphorus concentrations and remove 80% of suspended solids.
Describe how and where the project's black water is treated.
Black water is not treated on-site prior to discharge to the city sanitary sewer system. All laboratory lab waste passes through a ph neutralization treatment system before it is discharged to the city sanitary sewer system.
Metrics
Water use intensity (gal/sf/year)
Benchmark: 11.2
Predicted: 5.0
Measured: 4.6
Reduction in potable water use (from benchmark)
Predicted: 45.5%
Measured: 58.18%
Total annual water demand met using potable sources
Predicted: 47.2%
Measured: 44.7%
100% of stormwater is managed on-site.
Please explain if a mandatory metric is unavailable or a metric requires additional interpretive information.
Water reclaim from condensate is sent to the Harvard University District Energy Facility for use in its cooling towers. Data is not yet available for reclaim values.
A major theme of the project involved balancing the need for economy with the desire to build a facility capable of accommodating Harvard’s unforeseen scientific needs well into the coming century. The greatest impact on resource consumption comes from aggressively driving down the laboratory ventilation rates without sacrificing occupant safety and future flexibility. This effort began with Harvard’s first-ever Laboratory Ventilation Management Plan and with non-lab workstation environments segregated from labs and ventilated at significantly lower rates. This was coupled with a super-efficient Konvekta glycol runaround heat recovery system capable of achieving 80%–90% efficiencies. This proprietary energy-saving system has a four- to five-year payback.
The design team also analyzed the impact of a fully triple-glazed facade system against a more standard double-glazed system. While somewhat more expensive, the triple-glazed system performed at such a high level that perimeter heating could be eliminated from the design, which eliminated miles of piping and fin tube radiators that more than offset the additional cost. The façade’s fixed exterior shading system was critical to enabling the low-energy radiant technologies inside the building, minimizing solar heat gain, and enhancing daylight.
Design intent
How does this project contribute to local and/or disadvantaged economies?
The project team worked to meet the Boston Residents Jobs Policy goal of 50% Boston residents in the workforce and 25% of the total employee work hours going to people of color. The project achieved a workforce of 27% Boston residents and 30% people of color. Documentation was prepared describing the team's challenges and ultimate success in achieving the required procurement within the designated radii of the project, based on the sum of purchases, to meet the Living Building Challenge. The case study describes some exemplary achievements in preferring local suppliers, despite the project having started with a preference for some from European suppliers.
How did design choices reduce system sizes and minimize materials usage, allowing for lower cost and more efficiently designed systems/structure?
The fixed exterior shading system of the façade, which was critical to enabling the low-energy radiant technologies inside the building, minimizing solar heat gain, and enhancing daylight, combines solar control with material innovation. Utilizing hydroforming technology, the system was fabricated using 1.5 millimeter-thick stainless steel, a dramatic reduction in material mass and weight over a more conventional aluminum plate construction that had downstream benefits on the supporting substructure design and reactions at the connections to the building superstructure.
How did life cycle cost analysis influence the project's design?
It was determined that the high-efficiency Konvecta heat recovery system would offer first-year utility savings of over $1,000,000, compared to a typical heat recovery system. Despite its steep upfront cost, the system’s significant immediate cost savings, combined with the reduction in emissions, made it an obvious choice. Another LCA led to the development of the Harvard Laboratory Ventilation Management Plan, which optimizes the strict ventilation requirements in lab environments. The plan is predicted to save the university nearly $1,000,000 yearly and reduce greenhouse gas emissions by over 85,000 metric tons CO2e over the next 20 years.
Passive methods were an integral part of the design for the SEC. The custom-designed façade shading optimizes solar heat gain, reducing it during cooling periods and increasing it during heating periods. Furthermore, it is more efficient than typical fixed-system shading devices.
The above mentioned façade shading, in conjunction with triple-glazed windows and sky lighting, dramatically reduces the need for electrical lighting.
Multiple passive ventilation methods are utilized to minimize active ventilation throughout the building. All occupied spaces have user-operable windows, and the thermostats indicate the optimal conditions for opening windows. This increases the number of heating degree days for which natural ventilation can be used, thereby reducing the need for active ventilation. The first-of-its-kind laboratory ventilation plan further reduces active ventilation requirements by optimizing air use, recirculation, and air pathways.
These passive systems are supplemented by ultra-high-efficiency systems that together result in an energy use intensity, before considering renewables, that is roughly a quarter of that of a typical laboratory building.
Design intent
Describe any energy challenges associated with the building type, intensity of use, or hours of operation, and how the design responds to these challenges.
Laboratory buildings traditionally have extremely high energy use intensities in large part due to their need for high exhaust rates and plug loads. In addition to a high-performance façade and optimized solar shading, the design team and the owner’s Environmental, Health & Safety Department developed a lab ventilation management plan that aimed to reduce overall energy use by 30% in the labs while simultaneously improving occupant safety by instituting laboratory best practices. An extensive plug-load study was conducted at existing lab facilities on campus to validate design assumptions early in design.
Metrics
Is the building all-electric? No.
In its measured usage, including on-site renewables, did the project achieve its 2030 Commitment reduction target (70% reduction by 2015, 80% reduction by 2020)? Yes.
The project's total carbon (embodied + operational) over 10 years in kg CO2e is 63,262,297.
There is a 71% reduction (inclusive of renewables) from benchmark, measured.
0% of total energy is derived from renewable sources, measured.
There is a 19% reduction (inclusive of renewables) in operational carbon from benchmark, measured.
Please explain if a mandatory metrics is unavailable or a metric requires additional interpretive information.
The owner elected to install a rooftop PV array post-occupancy, and it became operational in September 2022. However, performance data is not yet available. Predicted on-site generation, provided by the installing contractor, is 184,000 kWh per year. This has been divided equally into 12 months and entered in the super spreadsheet. The final LEED Energy Report for the project reflected a proposed energy use intensity of 82 kBtu/sf/year, reflecting a 22% savings over ASHRAE 2010 with Appendix G.
Certified by the ILFI’s Living Building Challenge in the Materials, Beauty and Equity petals, the SEC has been acknowledged as Harvard University’s healthiest building. However, the project’s strategy to well-being goes well beyond eliminating chemical classes of concern within its interiors. The building was also carefully dimensioned to ensure high-quality daylighting in all regularly occupied spaces throughout the building, visual connections to nature, and access to fresh air. Operable windows in all perimeter spaces of the building introduce fresh air to the building interior, which is then cascaded via acoustically lined transfer devices to public corridors and walkways and ultimately to one of the two building-height atria where it is exhausted at the roof level. Deep carve-outs in the building’s floorplates adjacent to substantial glazed areas ensure daylight penetrates as far as possible into the building. Atrium spaces link researchers on different floors, and informal workspaces adjacent to circulation corridors offer opportunities for chance encounters and informal exchange. Special attention was paid to material in these spaces to ensure acoustical performance. This open, collaborative approach to the spaces in-between specific research initiatives fosters the school’s strong interdisciplinary culture and ensures that each research neighborhood within the building is active and integrated.
Explore the Harvard University Science and Engineering Complex’s Design for Well-being strategies in Fig. 3 Design for Well-being.
Design intent
Was a chemicals of concern list or other third-party framework used to inform material selection? If so, how?
All building products were reviewed in order to avoid ILFI Living Building Challenge Red List-containing chemical classes. The owner engaged a team of third-party experts in the field of material science and building construction to research specified products, inform the design team of alternative options, document vetted and acceptable products for the project during construction, and advocate in the marketplace for ingredient transparency and Red List-free products.
How did the project advocate for greater transparency in building material supply chains?
During the design and construction of this building, the team asked more than 1,200 companies to disclose information about over 6,000 products and asked for the chemical composition of every product used. Through the SEC’s massive buying power, this project significantly moved the market in a healthier direction. Many manufacturers reformulated their products for this project to eliminate chemicals of concern, some in perpetuity, and other manufacturers pursued product transparency labels, allowing future project teams to more easily assess ingredients and compare products.
Metrics
53% of the regularly occupied area is daylit (sDA 300/50%).
100% of the regularly occupied area is compliant with annual glare criteria (ASE 1000, 250).
68% of the regularly occupied area has quality views.
50% of the regularly occupied area has access to operable windows.
The design goal for maximum C02 is 1,000 ppm. The goal is relative to an absolute value.
Polished concrete floors, which also serve as building structure and provide radiant heating and cooling to the space, were chosen for all circulation spaces in the building. This eliminates additional mechanical systems and floor finishes for nearly 40% of the building area.
Over 10,000 square feet of reclaimed wood was used for flooring materials in the various classrooms in the project for its warm tone and aesthetic quality. To optimize the use of this valuable resource, the reclaimed wood was cut into veneers and applied to an FSC, formaldehyde-free plywood substrate and prefinished with a water-based, low-VOC coating.
Six waste streams, measured by weight, were managed on-site during construction. Five of the six streams diverted 100% of the wood, metal, paper/cardboard, drywall, and concrete for recycling. Composting containers were provided in construction worker eating areas as well as within the construction administration offices.
Material recycling and reuse were considered for the project for LBC Materials petal certification. The SEC building contains over 30 salvaged categories that were diverted from the landfill, including flooring, laboratory equipment, and interior landscaping material.
Design intent
Did embodied carbon considerations inform the design? How?
Life cycle analysis was conducted early in design to evaluate concrete and steel as the main structural system for the new building. Since the new above-grade building design had to adapt to the existing below-grade foundation and columns, a steel frame was selected to efficiently mitigate column grid transfers. Furthermore, multiple materials were evaluated for the façade shading screen. Stainless steel was selected for its strength and elasticity in the hydroforming process.
Did the idea of circularity/circular economy inform the design? How?
By salvaging and reusing building materials, the project diverted materials from the landfill and reduced the need to manufacture products, which will further reduce the carbon footprint of the building. Over several years, the project team, with the assistance of the Harvard Surplus Distribution Center, reviewed upcoming renovation and construction projects on the Harvard campus as well as local and regional outlets for possible sources of salvaged materials. Refinished wood benches, lockers, file cabinets, extinguisher cabinets, lighting, and cord reels are among the salvaged materials installed at the SEC.
Describe any special steps taken during design/construction to make disassembly, deconstruction, or reuse easier at the building’s end of life.
Laboratory spaces have exposed overhead systems and utilize an acoustic composite structural decking material that also provides channels for hangers and bracket attachments. Not only does the acoustic deck reduce the need to deconstruct and reinstall acoustic materials, but the hanger channels also allow overhead MEPFP attachments to be placed, removed, and reinstalled as the laboratory spaces are renovated over time.
Metrics
46% of project floor area was reused or adapted from existing buildings.
Was embodied carbon modeled? Yes.
36.5 kgCO2e/sf is the project’s embodied carbon intensity.
100% of the installed wood is FSC certified.
The laboratory spaces are organized to provide a blend of wet and dry lab services in regular, modular bays that enable future flexibility to accommodate new and evolving research pursuits. Lab systems have been organized using double-ended services at the end of the lab blocks to minimize service interruptions. Additionally, all air supply and exhaust systems feature bypass and isolation provisions to maintain system operation and minimize system shutdowns.
Backup energy generation to preserve critical research assets and building operations, in addition to legally required backup power, was strategically located at the District Energy Facility (DEF) to supply utility-level backup to the SEC building.
The building landscape and water systems have been designed to exceed local and state stormwater requirements and water conservation measures in anticipation of the changing climate. The building was raised two feet in order to withstand increased flooding and sea-level rise.
Explore the Harvard University Science and Engineering Complex’s Design for Change strategies, including sea level rise and flood mitigation, in Fig. 4 Design for Change.
Design intent
In what ways does the design anticipate climate change over the life of the building?
Given the project’s proximity to the Charles River, extensive research was conducted on the effects of climate change-related flooding on the site. The building was raised and critical infrastructure was either elevated or relocated to protect it from potential floodwaters, including 100-year levels. The Allston campus District Energy Facility (DEF), which was initially going to be located in the basement of the SEC, was relocated midway through the project to an off-site location where further robust and resilient provisions could be applied to the design.
How does the design anticipate restoring or adapting function in the face of stress or shock, such as natural disasters, blackouts, etc.?
Natural ventilation and building thermal mass were analyzed during design to optimize and project interior environment conditions during blackouts or District Energy Facility failure. Critical research and building infrastructure are on a local backup power supply that includes local UPS battery power for critical computing needs. The lower levels of the building are home to critical research facilities and building infrastructure spaces, which have been raised and compartmentalized with bulkhead flood barriers to protect them from possible external or internal flooding.
Metrics
Research Score: 70
Resiliency Score: 33
The building can be used as a safe harbor to support the community during a crisis. The building has robust flood proofing, passive design measures, and backup generation designed to enable it to withstand extreme events. Additionally, it has a significant amount of flexible space to accommodate crisis needs.
The SEC raised the bar for what can and should be expected of academic research facilities in terms of performance, occupant comfort, well-being, and materials responsibility without sacrificing research capabilities and flexibility. Several critical exercises were undertaken during the design process that were fundamental to properly designing the spaces and systems. Early shadow studies and an examination of the activities and working habits of the research community were undertaken to fully understand key facilities. The massive research effort that was undertaken as a prelude to the project’s LBC certification generated a materials database that serves future projects at all scales and motivated industries to change their manufacturing processes. The design team worked with the building operators to ensure that systems commissioning and early operation were as smooth as possible. That relationship continues to this day as additional fit-out and renovation work occurs.
“What’s impressive about this project are the implementation of new strategies and experimental technologies for a lab building that haven’t been used before, which really embody the Design for Discovery principle.”—Jury Comment
Design intent
What lessons learned through this project have been used to improve subsequent projects?
The pursuit of the ILFI Materials petal certification to remove Red List materials from the building products cannot be understated. This effort and commitment from the university and all project stakeholders required in-depth analysis of building product material composition, advocacy for material ingredient transparency, and the development of new construction administration workflows to ensure all building products were scrutinized and properly approved. This investment in knowledge, awareness of product ingredients, and advocacy in the marketplace will serve the client, construction team, and design team on future projects.
If a post-occupancy evaluation was conducted, describe the process and outcomes.
The university has conducted internal occupant surveys, which have been reported back to the design team. Users have expressed gratitude for the quality of space and access to light in their immediate work areas as well as shared common spaces. However, the natural ventilation in the atrium spaces was noted to be too windy and cold during certain conditions. The design team discovered that the atrium windows had been incorrectly programmed to fully open during natural ventilation (economizer) mode. However, the affected windows only needed to be partially opened to provide effective cross ventilation in the building.
If a post-occupancy performance testing was conducted, describe the process and outcomes.
The building operator is engaged in post-occupancy commissioning and optimization for building systems including, but not limited to, heat recovery, air handling, instrumentation, BMS monitoring, and irrigation programming. The design team has been reviewing trending data and providing feedback to the owner to assist in this effort, which has detected airflow monitoring sensors that required calibration, increased heat recovery efficiency to meet design targets, and optimized the watering schedule for the post-plant establishment period. The design team receives bimonthly utility-level data that is analyzed and reported back to the building operators to track building performance.
Metrics
Post-Occupancy Evaluation Score: 80
Transparency Score: 80
Commissioning Score: 80
Feedback Score: 40
Project team & Jury
Year of design completion: 2021
Year of substantial project completion: 2021
Gross conditioned floor area: 544,400 sq. ft.
Number of stories the building has: seven
Project site: brownfield
Project site context/setting: urban
Annual hours of operation: 4,745
Site area: 274,528 sq. ft.
Total annual users: 2,000
Code Consultancy: Code Red Consultants
Engineering - Climate: Transsolar Inc.
Engineering - Structural: Buro Happold
Façade: Knippers Helbig GmbH
General Contractor: Turner Construction Company
Signage, graphics: Ockert und Partner
Laboratory Planners: Jacobs Laboratory Planning Group
Landscape Architect: Stephen Stimson Associates
LBC Consultancy: Integrated Eco Strategy
LEED Consultancy: Harvard Office for Sustainability and Thorton Thomasetti
Lighting Design: Bartenbach GmbH and Lam Partners
MEP, Fire Protection: van Zelm Heywood & Shadford Inc.
Katie Ackerly, AIA, Chair, David Baker, Oakland, Calif.
Julian Owens, Assoc. AIA, Jacobs, Arlington, Va.
Seonhee Kim, AIA, Design Collective, Baltimore
Avinash Rajagopal, Metropolis, New York
The COTE® Top Ten Award is the industry’s best-known award program for sustainable design excellence.
Explore ten projects setting the standard in design and sustainability, presented by the Committee on the Environment.