RIDC Mill 19: Buildings A & B
The award-winning sustainable design of RIDC Mill 19: Buildings A & B transforms a former steel mill to welcome the sustainable future of advanced manufacturing.
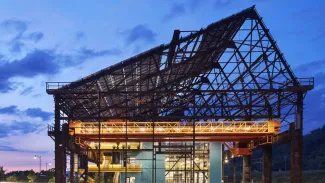
Project highlights: RIDC Mill 19: Buildings A & B
- Architecture Firm: MSR Design with R3A Architecture
- Owner: Regional Industrial Development Corporation (RIDC)
- Location: Pittsburgh, Pa.
- Project site: Brownfield
- Building program type(s): Education – College/University (campus-level), Office – 100,001 or greater, Public Assembly – General
A vital new addition to Pittsburgh’s post-industrial landscape, Mill 19 is a bold transformation of a former steel mill that now welcomes the sustainable future of advanced manufacturing. Within the decommissioned mill’s steel superstructure, multi-tenant, tech-focused buildings create tension between old and new, while the country’s largest single-slope bifacial glass photovoltaic array crowns the project. In addition to accelerating the city’s future, Mill 19 is a potent catalyst for the development of Hazelwood Green, Pittsburgh’s largest riverfront redevelopment project, which is being built on its final large-scale brownfield site.
AIA Framework for Design Excellence principles
From industry to innovation
Mill 19 is an emblem of Pittsburgh’s transformation from its industrial steel-making past to a future of sustainable advanced manufacturing. Through a bold approach to adaptive reuse, the project viscerally interweaves new space for the city’s robotics industry within the ruins of a decommissioned steel mill. The project welcomes the public through a series of linked exterior experiences framed between the 1,360-foot-long existing steel superstructure and three multi-tenant tech buildings within it. The design team prioritized experiential sustainable design strategies, including capping the existing structure with the country’s largest single-slope bifacial glass PV array and designing a performative landscape that collects, manages, and harvests an immense volume of rainwater.
History
Mill 19 re-inhabits the last remnant of the former Pittsburgh Jones & Laughlin Steel Company. Built in 1953, the original structure operated as a steel rolling mill until the entire complex ceased production in 1997. Today, Mill 19 is the heart of Hazlewood Green, the city’s largest riverfront redevelopment project, located on its last remaining large-scale brownfield site. As the first completed project within Hazelwood Green, Mill 19 sets the tone for the redevelopment of all 178 acres into a sustainable, mixed-use, high-tech innovation district that reconnects surrounding neighborhoods to the river’s edge.
Box within a shell
The design team took a unique approach to adaptive reuse by peeling away the existing mill’s deteriorated sheet metal skin, exposing its dramatic steel skeleton, and installing a sequence of speculative high-tech office, lab, and manufacturing structures within the existing structural frame. Old and new are clearly differentiated as the project leverages the interplay between industrial and human scales.
Explore the adaptive reuse strategies to the Mill's sheet metal skin in Fig. 1 Design for Integration.
The post-industrial promenade
Serving as the experiential heart of Mill 19, a full-height corridor of open public space runs the length of the project between the new buildings and the existing frame. Walkways, balconies, and stairways invite the public to explore the curated void. Daylight filters through the bifacial glass PV panels above to illuminate a landscape that features concrete block and steel elements salvaged from the original structure. Rain gardens, native plants, and elevated pathways delineate spaces for a range of experiences, from individual contemplation to large-scale community gatherings.
AIA Framework for Design Excellence
Transformational design goals for Mill 19 focused on integrating building performance into all aspects of the project. The client and design team established ambitious energy, water, and daylight performance targets at the start of the project and stewarded them through continuous iterative analysis. Designing for discovery and change stemmed directly from the focus on the project’s physical history and future trajectory. The project accomplishes impressive levels of experiential, sustainable performance within the financial constraints of a speculative core and shell commercial development.
Identity
In the Winter 2020 Pittsburgh Quarterly, Charles Rosenblum writes, “[Mill 19] is all Pittsburgh. Where else can you find so compelling an architectural embodiment of high-tech resurgence and ecological landscape within the mammoth rusty ruins? And what combination better unites the historical and forward-looking currents of our identity?”
Please explain if a mandatory metric is unavailable or requires additional interpretive information.
Mill 19 is a site-specific phased speculative development that began concept design in 2015. Building A, its surrounding site, and the full photovoltaic canopy was completed in 2017. Building B and its surrounding site was completed in 2019. Building C and its surrounding site is currently under construction with a projected 2023 completion date. All submitted metrics including the COTE Super Spreadsheet are for Building A, Building B, and their respective surrounding landscape areas. The full photovoltaic array is also included in relevant metrics. Building C and its associated landscape is excluded from all submitted metrics.
Mill 19 is one of the last artifacts of a golden era of industry that created thriving communities built on economic stability. The closure of the last operating steel mill in Pittsburgh left the community’s residents uncertain about the future. Mill 19 provides community-facing spaces that engage the residents who have felt excluded from recent economic progress. The public spaces at Mill 19 that evoke communal ownership, healing, and pride in their heritage.
Mill 19’s central design concept of constructing new buildings within the historic shell prioritizes public use in a traditionally insular project typology. As a core and shell, speculative, high-tech commercial development with security and intellectual property concerns, Mill 19 maintains privacy for the innovative companies inside while providing dramatic exterior public spaces grounded in the history of the site. The promenade, a ribbon of mediating softscape, is fully accessible and walkable, inviting continuous movement. It terminates at a voluminous plaza for community events located in the last three structural bays of the existing superstructure and opens onto the adjacent public park.
Design intent
Who does the project serve? Identify the stakeholders who are directly or indirectly impacted by the project.
The challenge from the beginning has been balancing the program of the buildings as incubators for advanced research within a community that has its own special skillsets. While somewhat restricted by the tenant-stakeholders, Mill 19’s greatest achievement is providing public spaces for Hazelwood residents to celebrate their shared passions. This facilitates greater access to the waterfront, green space, and local trails. In the future, as the entire 178-acre site is developed, new stakeholders will become permanent neighbors and integrate with the existing community.
Describe the stakeholder engagement process over the course of the project.
Both the Mill 19 project and the Hazelwood Green development engaged the community regularly through neighborhood organization meetings, special engagement events, and organizing workshops for the public art process, the artist for which was selected by the community. At the request of the residents at these meetings, the contractors for each phase reached out to local residents about available jobs. The overall process uncovered the deep-rooted relationship between the former steel mill and the community still recovering from its closure—and their worries that gentrification would disrupt their neighborhood.
Identify project goals that support equitable communities and describe how those goals were developed.
Before a project can begin to provide a space for healing, it must first resolve to create no further harm. Bringing new life to the site meant ensuring we weren’t unintentionally driving away longtime residents who are the fabric of Hazelwood. If the space was not accepted by the community, then the project would be a failure. As a commercial core and shell project, control over tenant leasing would be limited; however, through design, Mill 19 offers a vision of access, opportunity, and identity. This is the community’s mill, their history, and it will remain so for generations to come.
Describe the project team's explorations or design strategies that respond to the above-stated goals.
Accessible spaces at Mill 19 mean more than simply accessible routes. They offer invitations to explore, a sense of safety, and personal connections to the place. They generate human-scale moments in a monumental setting and respect the existing structural forms through selective intervention. Accessible also means facilitating spaces that bring workforce training so that the community can gain the skills needed in this next industrial era. It means cleaning heavy metals from the soil and unburdening the community stormwater system to provide a cleaner, safer environment for play and inhabitation.
Describe stories or evidence that demonstrate how the project successfully contributes toward more equitable communities.
Since opening the first phase in 2019, Mill 19 has successfully drawn the community to the site. Throughout the pandemic, it was a backdrop for distanced community theater and film. The south plaza seamlessly integrates with the adjacent public park, so much so that events hosted in one bleed into the other, creating a blurred line between the park and the privately developed landmark. Residents continue to gather regularly as COVID measures have lifted to share poetry, music, and culture, fostered by local organizations that leverage the spaces under the photovoltaic shed roof.
Every community is unique, and every project has unique opportunities to respond to issues of equity and inclusion. Describe any exemplary practices or outcomes for this project.
For over a century, the Jones and Laughlin steel mill supplied materials to an expanding nation. The railroading, coal, steel, and aluminum industries all helped establish Pittsburgh as a flourishing metropolis given its location near the coal fields and confluence of rivers that ferried barges of raw materials. At the same time, however, economic inequality was rooted in this growth, embodied by the Gilded Age tycoons of Andrew Carnegie and Henry Clay Frick, whose names adorn monuments throughout the city. However, this was also the home of the Homestead Massacre in 1892, and the legacy of labor rights and inequality persists today as neighborhoods around the city have unequally benefited from the institutions driving policy. The pride and identity within each neighborhood are remarkably strong, and recognizing this has always been a priority for the design of Mill 19. Community members repeatedly voiced concern about wealthy interests encroaching on their Hazelwood neighborhood.
Decommissioned, derelict, and otherwise abandoned post-industrial sites can be painful reminders to the communities in which they sit of a world that has moved on. Not only are they physically hazardous as ruins, but they often have ongoing contaminants impacting the ecology and health of the community. Expensive remediation is an obstacle to redevelopment, and Mill 19 provides a template for other market-rate commercial developments. The result is a respectful, transformed monument that can be claimed by the current residents as their own.
This project transformed a former industrial steel mill that was once a source of significant environmental pollution and ecological contamination into a regenerative site. The project focused on greater biodiversity through the careful selection of resilient native plant species and the natural return of native creatures to inhabit the large, vegetated open space. The hardy plants selected can handle stressful weather conditions and alleviate the damaging ecological impact of stormwater runoff off-site. Several paths in, around, and through the landscape bring visitors into direct relationships with the vegetation and showcase the many ways the design has prioritized the regional ecosystem.
Spontaneous plant species such as sumac, black locust, willow, quaking aspen, ferns, and sedges form the backbone of an array of wild gardens. The planting design embodies the unruly and tenacious qualities of post-industrial landscapes, providing substantial cost-effective ecological services that are low maintenance. The design integrates aggressive disturbance-adapted species that store carbon at a faster rate with slow-growing native species that sequester considerable amounts of carbon over time.
Explore RIDC Mill’s different tree and plant species as well as a diagram of the stormwater infiltration, storage, and reuse in Fig. 2 Design for Ecosystems.
Design intent
How does the design minimize negative impacts on animals?
The site design minimizes negative impacts on animals through sensitive dark sky lighting design and wetland habitat. Illumination is provided in primary public use areas in the south porch, egress stairs and bridges, and the loggia. This approach leaves the channel and adjacent plantings undisturbed, providing viable habitat for birds, bats, and other wildlife while allowing enough light so that the site feels secure and navigable.
Wetland habitats are vital aspects of the environment due to their shallow water levels and high quantity of nutrients. They are an important food source for organisms at the base of the food web.
How does the project support biodiversity and improve ecosystem services?
The project supports biodiversity through the integration of native planting gardens focused on carbon sequestration, pollinator habitat, and water quality improvement. The design integrates disturbance-adapted species that store carbon at a faster rate along with long-living native species that sequester high amounts of carbon over time. A 12-foot wide by 400-foot long water channel filters rainwater through wetland retention basins and infiltration gardens that support birds, amphibians, and insects. Pollinator-friendly native plant species like sumac, black locust, serviceberry, and little bluestem diversify food sources for a range of wildlife, providing substantial ecological services that are low maintenance and low cost.
Metrics
0% of site area was vegetated (landscape or green roof) pre-development.
14.9% of the site area is vegetated (landscape or green roof) post-development.
There was a 100% increase in vegetated area, post-development.
100% of the vegetated areas are planted with native species.
The inability to infiltrate stormwater above contaminated soils was the site’s most significant constraint and greatest opportunity. The team designed a 12-foot-wide water channel that flanks the entire western façade of the mill. The channel carries water from the contaminated soils and visibly conveys 1.1 million gallons of rainwater through a sequence of wetland retention basins and infiltration gardens. Overflow from larger rain events is collected in a dedicated underground cistern to refill the water features. The combination of infiltration, storage, retention, and evaporation allows an enormous amount of surface water retention before diversion to the nearby neighborhood district retention pond. Overall, through these combined strategies, 87% of the stormwater is managed on-site.
Rainwater is also collected from the roofs of the interior buildings into cisterns and is filtered for reuse in the facilities’ restroom flushing fixtures. The collected water is also available for use in the campus evaporative cooling towers, which reduces the mechanical systems’ demand for potable water by 1 million gallons per year. These strategies are designed to reduce Mill 19’s potable water use by up to 52%.
Design intent
Describe how the project's stormwater and potable water strategies contribute to site and community resilience.
Mill 19 addresses three related resilience design challenges: remediating and redeveloping a brownfield site, protecting the adjacent river through on-site stormwater management, and recharging aquifers through potable water use reductions, including rainwater capture, filtration, and reuse. The site’s contaminated soils made infiltration impossible in areas, leading to a design that celebrates the conveyance, capture, and infiltration of stormwater along its quarter-mile length. This approach enables Mill 19 to steward water as a critical resource and, through its interweaving of public space within its water management strategies, to demonstrate the profound beauty these strategies can create.
Describe the quality of the water that runs off the site.
Mill 19 manages 87% of its stormwater on-site. The water that does run off-site is high quality, having already gone through extensive natural filtration along the project’s stormwater conveyance system, which includes bioswales and retention ponds. Landscape plantings prioritize disturbance-adapted species to create wild, performative gardens. The vast majority of on-site rainfall first encounters the clean surfaces of Mill 19’s photovoltaic array or membrane roofs before being redirected into the extensive stormwater management features. All off-site water runs to a neighborhood infiltration basin.
Describe how and where the project's black water is treated.
Black water treatment relies on conventional municipal waste treatment facilities.
Metrics
Water use intensity (gal/sf/year)
Benchmark: 17.9
Predicted: 4.9
Measured: 6.8
Reduction in potable water use (from benchmark)
Predicted: 72.5%
Measured: 95.1%
Total annual water demand met using potable sources
Predicted: 43.8%
Measured: 61.8%
86.8% of stormwater is managed on-site.
Viable speculative office buildings must be able to meet or exceed the market demand for commercial space; therefore, excessive materials and waste need to be kept to a minimum to remain competitive. The project went through rigorous planning and several full schematic designs to explore and strike the right balance between a project that would do justice to the historic mill structure while remaining within the financial means of the nonprofit client. The project’s interior buildings were designed and constructed in succession over seven years, ensuring that the team could design to current market conditions while also applying lessons learned from previous phases.
The size and shell of the building were optimized to anticipate tenant requirements and cost-saving build-outs. Mechanical and electrical systems were designed, evaluated, and selected to reduce energy use for greater cost savings for both the client and tenants. The project’s shared water loops leverage an economy of scale to generate heating and cooling across multiple buildings to maximize energy performance and lower costs.
Design intent
How does this project contribute to local and/or disadvantaged economies?
Mill 19 is the headquarters for Catalyst Connection, a private nonprofit organization that retrains local workers to equip them with the skills needed to support the continued growth of new manufacturing in southwestern Pennsylvania. Catalyst Connection provides state-registered apprenticeships for entry-level manufacturing technology workers, student engagement, and worker training, assessment, and certification systems. The client made a concerted effort to use local construction labor by focusing on outreach and lowering bars to entry like paying for union dues. All screening fencing on Mill 19’s east side was supplied and installed by a manufacturer located in the project’s Hazlewood neighborhood.
How did design choices reduce system sizes and minimize materials usage, allowing for lower cost and more efficiently designed systems/structure?
Designing speculative commercial buildings within an existing steel shell mandated material and structural efficiency. The team balanced tenant expectations for floor-to-floor heights, structural bay clearances, and daylight and views within the existing armature’s fixed volumetric capacity for construction. The increased first-floor height was based on the maximum glazing height available to reduce waste from jumbo glass. The heights of levels two and three are set by the maximum metal panel height. Glazing width decisions were informed both by daylight analysis and alignment with the adjacent metal panel’s 30-inch module.
How did life cycle cost analysis influence the project's design?
Speculative commercial development foregrounds life cycle cost analysis. Initial costs must be managed to fit the development pro forma, while utility and maintenance costs must be understood and accepted by future tenants. The project’s campus approach to HVAC required a higher initial investment for a long-term reduction in energy costs for tenants. The team prioritized durability in exterior material and planting selections for the core and shell project. The reduced life cycle costs resulted in acceptable payback windows for the increased first costs of the project’s metal panel cladding, metal stairs and bridges, and hearty disturbance-adapted plantings.
Cost
$272 per square foot
The passive design goal of minimizing the project’s conditioned interior volumes influenced the decision to insert new buildings within the existing steel structure. The design used energy and daylight analyses to vet the initial parti, optimize the glazing ratio, and develop an airtight envelope with insulation levels slightly above code in the interior-load-dominated buildings.
A central mechanical plant provides a shared water loop for efficient heating and cooling. This system meets the project’s immediate energy needs while facilitating a switch to future planned district energy connections. The mechanical systems are entirely electric. Energy recovery ventilation and efficient lighting design further minimize the project’s energy demand. All the buildings’ electrical subpanels are intelligently metered and integrated into the building’s automation system to provide feedback to the owner and the public on energy use across the campus.
Mill 19 features a monumental 2 MW solar array designed to generate enough energy to exceed the anticipated demand for the first two interior buildings. A bifacial glass array, mounted on the southwest slope of the existing steel structure, simultaneously converts direct sunlight and light reflected from the interior roofs into energy and creates an evocative atmosphere of dappled light below.
Design intent
The passive design goal of minimizing the project’s conditioned interior volumes influenced the decision to insert new buildings within the existing steel structure. The design used energy and daylight analyses to vet the initial parti, optimize the glazing ratio, and develop an airtight envelope with insulation levels slightly above code in the interior-load-dominated buildings.
A central mechanical plant provides a shared water loop for efficient heating and cooling. This system meets the project’s immediate energy needs while facilitating a switch to future planned district energy connections. The mechanical systems are entirely electric. Energy recovery ventilation and efficient lighting design further minimize the project’s energy demand. All the buildings’ electrical subpanels are intelligently metered and integrated into the building’s automation system to provide feedback to the owner and the public on energy use across the campus.
Mill 19 features a monumental 2 MW solar array designed to generate enough energy to exceed the anticipated demand for the first two interior buildings. A bifacial glass array, mounted on the southwest slope of the existing steel structure, simultaneously converts direct sunlight and light reflected from the interior roofs into energy and creates an evocative atmosphere of dappled light below.
Design intent
Describe any energy challenges associated with the building type, intensity of use, or hours of operation, and how the design responds to these challenges.
As a core and shell speculative commercial development for Pittsburgh’s high-tech robotics industry, it was a challenge to establish predicted internal energy loads. In response, the team developed a user profile for energy demand that was between that of typical office space and energy-intensive research and development activities. These internal load assumptions were consistently depicted as the visually muted, static base of energy use bar graphs when analyzing optimization strategies. The team then prioritized and presented sequential optimization efforts from the outside in with an optimized envelope, efficient HVAC systems and energy efficiency measures, and efficient lighting design.
Metrics
Is the building all-electric? No.
In its measured usage, including on-site renewables, did the project achieve its 2030 Commitment reduction target (70% reduction by 2015, 80% reduction by 2020)? Yes.
The project's total carbon (embodied + operational) over 10 years in kg CO2e is 15,883,600.
There is an 82.8% reduction (inclusive of renewables) from benchmark, measured.
66% of total energy is derived from renewable sources, measured.
There is a 95% reduction (inclusive of renewables) in operational carbon from benchmark, measured.
As a core and shell speculative commercial development for Pittsburgh’s high-tech robotics industry, it was a challenge to establish predicted internal energy loads. In response, the team developed a user profile for energy demand that was between that of typical office space and energy-intensive research and development activities. These internal load assumptions were consistently depicted as the visually muted, static base of energy use bar graphs when analyzing optimization strategies. The team then prioritized and presented sequential optimization efforts from the outside in with an optimized envelope, efficient HVAC systems and energy efficiency measures, and efficient lighting design.
Metrics
Is the building all-electric? No.
In its measured usage, including on-site renewables, did the project achieve its 2030 Commitment reduction target (70% reduction by 2015, 80% reduction by 2020)? Yes.
The project's total carbon (embodied + operational) over 10 years in kg CO2e is 15,883,600.
There is an 82.8% reduction (inclusive of renewables) from benchmark, measured.
66% of total energy is derived from renewable sources, measured.
There is a 95% reduction (inclusive of renewables) in operational carbon from benchmark, measured.
Mill 19 blends an extensive array of outdoor circulation and gathering space into a traditionally insular project typology. A quarter-mile-long loggia runs the full length of the project, threading a range of public spaces along the west façade that adapt and respond to the exoskeleton’s unique conditions to create occupiable platforms, furnished gathering spaces, stepped terraces, sunken sun decks, and floating walkways. Dynamic yellow bridges, stairs, and overlooks stitched into and from the exoskeleton connect to the loggia below and provide spectacular views of downtown Pittsburgh and the Monongahela River. Seamless detailing integrates the stairs, walkways, and bridges into the new architecture, the exoskeleton, and the landscape. These elements enable visitors to move through a variety of conditions and experiences, inviting them to climb, descend, hover, jump, cross, overlook, rest, and explore.
Extensive daylighting studies informed the floor plate width, glazing area, and glazing distribution to achieve the project’s goal of 65% spatial daylight autonomy. Celebrated main internal stairs animate the west façade and encourage active circulation. Mill 19’s exterior and interior features provide experiences and views that engender a deep connection to the unique surrounding context.
Design intent
Was a chemicals of concern list or other third-party framework used to inform material selection? If so, how?
The design team used the Living Building Challenge Red List to prioritize Red List-free materials. The project used a waterborne spray foam after first limiting its use to necessary exterior envelope connection details. Fluropon Pure, a Red List-compliant metal panel color and finish coating, was used in the project’s third phase after the design team worked directly with metal panel manufacturers and coating manufacturers.
How did the project advocate for greater transparency in building material supply chains?
The design team was responsible for improving the transparency and sustainability of metal panel coatings through sustained advocacy. During the project’s first phase, the metallic Red List-free exterior metal panel coating finish was not available. The team coordinated discussions between Sherwin Williams, producers of the Red List-free coil and extrusion coating Fluropon Pure, and the metal panel manufacturers. After six years and two project phases of continued advocacy, the Fluropon Pure in a metallic finish became commercially available and is now being used in the construction of Mill 19’s third phase.
Metrics
66% of the regularly occupied area is daylit (sDA 300/50%).
0% of the regularly occupied area is compliant with annual glare criteria (ASE 1000, 250).
88% of the regularly occupied area has quality views.
0% of the regularly occupied area has access to operable windows.
The design goal for maximum C02 is 700 ppm. The goal is relative to outdoor CO2 levels.
Please explain if a mandatory is unavailable or a metric requires additional interpretive information.
The regularly occupied area that is compliant with annual glare criteria (ASE 1000, 250) has not been assessed because the buildings are core and shell structures with operable glare reduction mitigation provided by individual tenant fit-outs.
The innovative reuse of existing site materials grounds the project’s post-industrial identity, reduces its embodied carbon footprint, and minimizes demolition and construction waste. The existing monolithic structure’s individual bays are nuanced and unique, inspiring a customized approach for how the project and its users flow through it. The design team began the project by identifying opportunities within the extant steel exoskeleton to remove dangerous pieces and create sufficient openings for emergency access and windows. The design team carefully inventoried, labeled, and stockpiled salvaged steel so that they could be cleaned, cut, and reassembled as custom furniture elements, retaining walls for terraces, and railings.
“This project’s design for resources is really well thought out. For example, the public promenade contributes to the business, while also having a clear purpose, intending to both bring people into this piece of infrastructure and being an attractive asset for tenants.”—Jury comment
The design repurposes the original concrete slab into 5-foot by 5-foot cut slabs for stepped terraces, 8-inch by 6-foot decorative rail ties, and crushed rubble at three different scales for informal surfacing materials and as a ruderal base for the disturbance-adapted plantings. Bunker blocks collected from the site and reclaimed limestone boulders from the old retaining wall on 2nd Avenue, at the edge of the Hazelwood Green property, frame and create bridges across the rectangular water channel, form accessible sloped walkways, and define terraces for expanded gathering areas.
Explore how RIDC Mill’s materials were salvaged, reused, salvaged in place, and salvaged, stockpiled for future use in Fig. 3 Design for Resources.
Design intent
Did embodied carbon considerations inform the design? How?
Embodied carbon considerations were embedded in the project’s overall design, which sought to celebrate the site’s history through the creation of a post-industrial landscape. The most visible strategy is the reuse of the historic mill’s steel superstructure. The majority of the original steel and concrete elements that were selectively demoed to create paths in, around, and through the monolithic structure were cataloged, prepped, and reused in the site design. The planting selections integrate aggressive disturbance-adapted species that store carbon at a faster rate with slow-growing native species that sequester considerable amounts of carbon over time.
Did the idea of circularity/circular economy inform the design? How?
Mill 19 is a celebration of an idea embedded in circularity: Architecture should envision individual projects as temporary answers to temporary needs whose permanence come from their eventual use as material banks in a continuous cycle of reuse. The design’s identity is grounded in the dramatic exposing of a historic industrial structure. Its post-industrial character is derived from exploring the tension between new and old. Existing materials were extensively repurposed into landscape elements that invite public interaction. The project’s new buildings follow suit, prioritizing materials and construction methods that can be disassembled and reused on future projects.
Describe any special steps taken during design/construction to make disassembly, deconstruction, or reuse easier at the building's end of life.
Mill 19’s site context influenced its approach to designing for disassembly. The original mill’s construction consisted mainly of metal elements with exposed fasteners, including corrugated metal panels and a steel structure. The team maintained this tectonic in the design of the project’s new buildings and exterior platforms, bridges, and stairs. The project’s new wall sections have reasonable accommodations for disassembly, including simple, discrete, mechanically fastened layers. Spray foam is minimized through the use of continuous rigid mineral wool on the outside of the structural cavity. Metal panels with mechanically fastened attachments are used at all opaque wall assemblies.
Metrics
0% of project floor area was reused or adapted from existing buildings.
Was embodied carbon modeled? Yes.
28.4 kgCO2e/sf is the project's embodied carbon intensity.
None of the installed wood is FSC certified.
The Mill 19 project epitomizes a trajectory of past, present, and future change. The project transformed the existing mill structure into as a dynamic setting for high-tech advanced manufacturing, and the highly adaptable interior buildings are designed specifically for future change. As speculative office buildings focused on research and emerging technologies, they can be adapted to meet a wide range of future tenant needs and specialization. To support this type of reconfiguration and ensure that flexibility does not come at the expense of waste, the project is not overdesigned. The ground floor is designed to be easily modified to add loading berths and heightened glazing transparency in anticipation of neighborhood changes over the next 20 years. Abundant daylight is selectively screened by tenants on a space-by-space basis to provide immediate security to sensitive intellectual property while anticipating future uses with different privacy requirements. The location and number of interior and exterior egress stairs allow further resilience for interior demising options and a greater degree of flexibility to accommodate large and small tenant spaces.
Explore how Mill 19 reinhabits the last remnant of the former Pittsburgh Jones & Laughlin Steel Company in Fig. 4 Design for Change.
Design intent
In what ways does the design anticipate climate change over the life of the building?
Mill 19 prioritizes passive design to reduce energy demand, increase indoor environmental quality, and help anticipate climate change. Interior floor plate widths and window-to-wall ratios were designed to maintain interior daylighting levels through perimeter daylight penetration. The project’s bi-facial glass photovoltaic array helps control solar gain in the summer. And Mill 19’s new interior-load-dominated buildings feature envelopes designed to prioritize air tightness and long-term moisture control and only use continuous, moisture-resistant insulation outside of the structural cavity. These passive strategies help Mill 19 provide energy-efficient conditioned space based on current and anticipated climactic conditions.
How does the design anticipate restoring or adapting function in the face of stress or shock, such as natural disasters, blackouts, etc.?
The project’s emphasis on passive design provides limited baseline passive survivability. Partial backup power through fossil fuel generators is also provided. With its monumental photovoltaic array, robust off-grid functionality could be facilitated, but the project does not have any current or planned battery storage at this time.
Metrics
Research score: 80
Resiliency score: 33
The building cannot be used as a safe harbor to support the community during a crisis.
Through passive sustainability, the building can function for 24 hours.
The project was developed across three phases and over seven years. Therefore, each subsequent building has evolved based on what was learned in the previous phases for improved constructability, efficiency, operations, and performance. Updated products in building insulation, metal coatings, and other materials that were not available for the first phase have been incorporated into the later project phases. Assemblies that did not perform to the standards set for the project were modified to better integrate into the construction.
Project tours are regularly given on-site, both specifically about Mill 19 and as a major stop on tours of the greater Hazelwood Green development. These tours focus primarily on the challenges and successes of its environmental impact. A real-time energy output of the solar array can be viewed by anyone online via the Mill 19 solar monitor, and the array itself has been widely promoted and publicized as a case study to encourage solar renewable energy investment in the region. The success of Mill 19 has made it both a landmark and a venue to host international conferences, including two public addresses by President Joe Biden.
Design intent
What lessons learned through this project have been used to improve subsequent projects?
Due to the project’s phased development, lessons learned in detailing were actively implemented in later phases. An expression of vertical steel fins flanking glazing is present throughout the design, and the connection detail and blocking support of the aerogel thermal breaks for the fins was improved in each phase. On Building B, the detail was updated based on construction sequencing feedback from Building A. On Building C, the rough opening sizes were increased while modeling and dimensioning the rough and finished openings of all glazed areas to further improve the constructability of the critical detail.
If a post-occupancy evaluation was conducted, describe the process and outcomes.
A post-occupancy evaluation has not been performed.
If a post-occupancy performance testing was conducted, describe the process and outcomes.
A post-occupancy evaluation has not been performed.
Metrics
Post-occupancy evaluation score: 50
Transparency score: 60
Commissioning score: 100
Feedback score: 100
Project team & Jury
Year of design completion: 2018
Year of substantial project completion: 2020
Gross conditioned floor area: 166,900 sq. ft.
Number of stories the building has: three
Project site: Brownfield
Project site context/setting: Urban
Annual hours of operation: 2,424
Site area: 218,309 sq. ft.
Cost of construction, excluding furnishing: $45,400,000
Total annual users: 16,1196
Associate Architect: R3A Architecture
Building Envelope Commissioning: Intertek
Construction Manager: Turner Construction Company, Jendoco Construction Corporation, PJ Dick
Design Consultant: Atelier Ten, Inc.
Engineer - Civil: Lennon, Smith, Souleret Engineering, Inc., KU Resources
Engineer - Electrical and Plumbing: Bala Consulting Engineers, Inc.
Engineer - Structural: Bala Consulting Engineers, Inc., WZG Structural Consulting Engineers
Landscape Architect: TEN x TEN Studio
Lighting Consultant: Mazzetti
Technology Specialist: True North Consulting Group
Katie Ackerly, AIA, Chair, David Baker, Oakland, Calif.
Julian Owens, Assoc. AIA, Jacobs, Arlington, Va.
Seonhee Kim, AIA, Design Collective, Baltimore
Avinash Rajagopal, Metropolis, New York
The COTE® Top Ten Award is the industry’s best-known award program for sustainable design excellence.
Explore ten projects setting the standard in design and sustainability, presented by the Committee on the Environment.